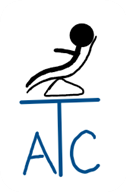
Problem Statement
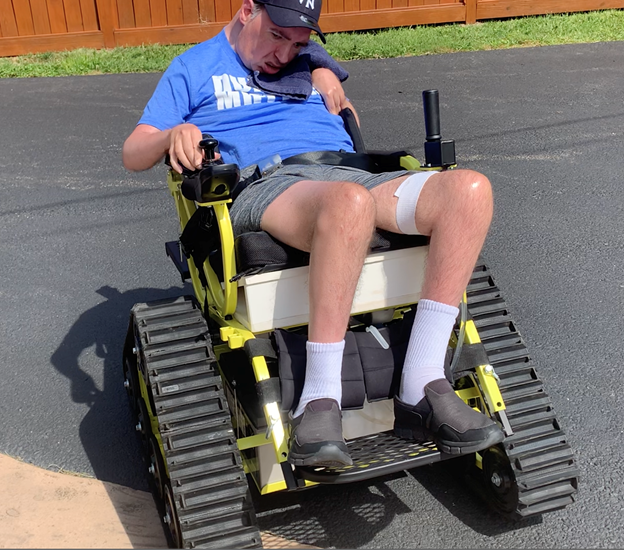
The Action Trackchair is an all-terrain powered wheelchair for those who are unable to control the wheelchair with the joystick on the right armrest. Our customer, Mr. Soles has a brother who is unable to control the joystick by himself due to a traumatic brain injury. The current attendant (caretaker) controller on the ATC is wired to the back of the wheelchair; thus, it requires the caretaker to stay inconveniently close to the wheelchair. The goal of this project is to design a wireless approach to control the wheelchair so the caretaker is not forced to stay right next to the wheelchair.
Here, the ATC is moving with the use of the attendant controller. As you can see, our team member, Eric, is staying very close to the chair and taking very small steps to make sure he is in range of the wheelchair.
Our Goals
- Needs:
- Wide range reception – The controller needs to be usable at least 5 feet away and a maximum range of around 30 feet.
- Safety – ATC will react to the controller correctly and will not put the rider in a dangerous situation when disconnected.
- Full mobility/Intuitive – The controller can move the ATC in all directions and is easy to use for the caretaker.
- Reliable – the ATC is being used for around 3-4 hours at a time so our device needs have a battery life that lasts that long.
- Wants:
- Rechargeable
- Compatible with other wheelchairs
System Design
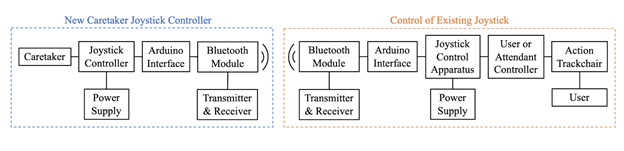
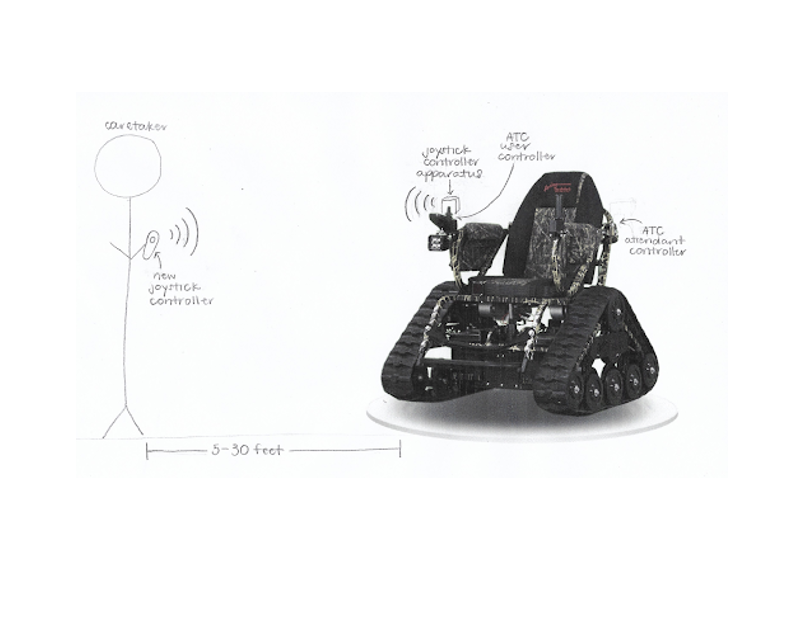
Final Prototype
Different components of our final prototype are given below. The novel attendant controller shown below will connect using Bluetooth to the steeper motors mounted on the physical apparatus. The controller will send a signal to control the motors which will then move different parts of the physical apparatus to generate the desired motion and control the user controller.
Novel Attendant Controller



Above shows the final prototype of the controller for our device. The battery, Bluetooth module, charging module, and microcontroller is able to fit nicely inside the controller shell. By pressing the button on the front of the device, information can be sent through the Bluetooth module to control the wheelchair.
Bluetooth Connection



Stepper motor remotely controlled by joystick through Bluetooth.
Stepper Motors


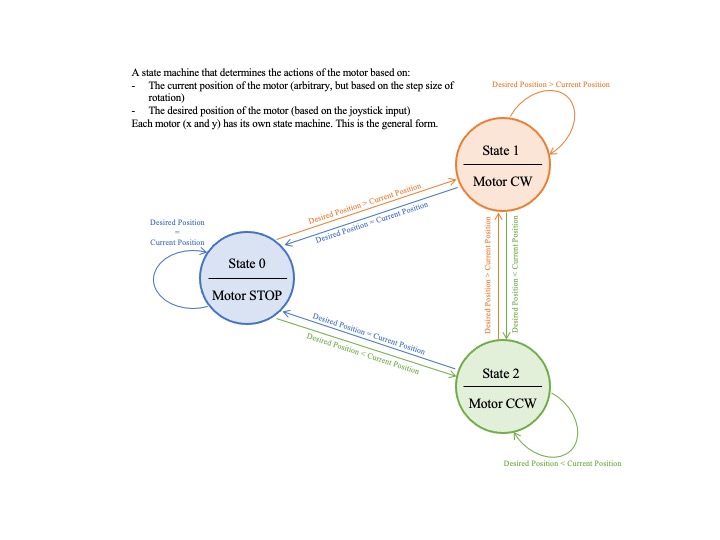
X and Y motors shown separately: X in a full rotation and Y in a partial rotation.
The motors continue to rotate to the desired position, as long as the joystick remains in the same position. Once the desired position is reached, the motors stop and remain stopped until the joystick position changes. If the desired position changes (joystick moves) before the original desired position is reached, the motor will start to approach the new desired position.
X and Y motors working together.
Physical Apparatus






Pictures above show a prototype of the physical apparatus that generates motion in the x and y-axis using two rotational motor. These components are made from a slippery plastic known as UHMW Polyethylene Plastic.
Previous Prototypes
Implementation of push button on new controller that only allows for control of the ATC when the button is pushed.
Servo motor remotely controlled by joystick through bluetooth

Stepper motor controlled by push button.
Stepper motor controlled by joystick: 4 basic cartesian directions (right, left, up, down).



1 of 2 physical apparatus prototypes involving two interlocking arms surrounding the joystick.
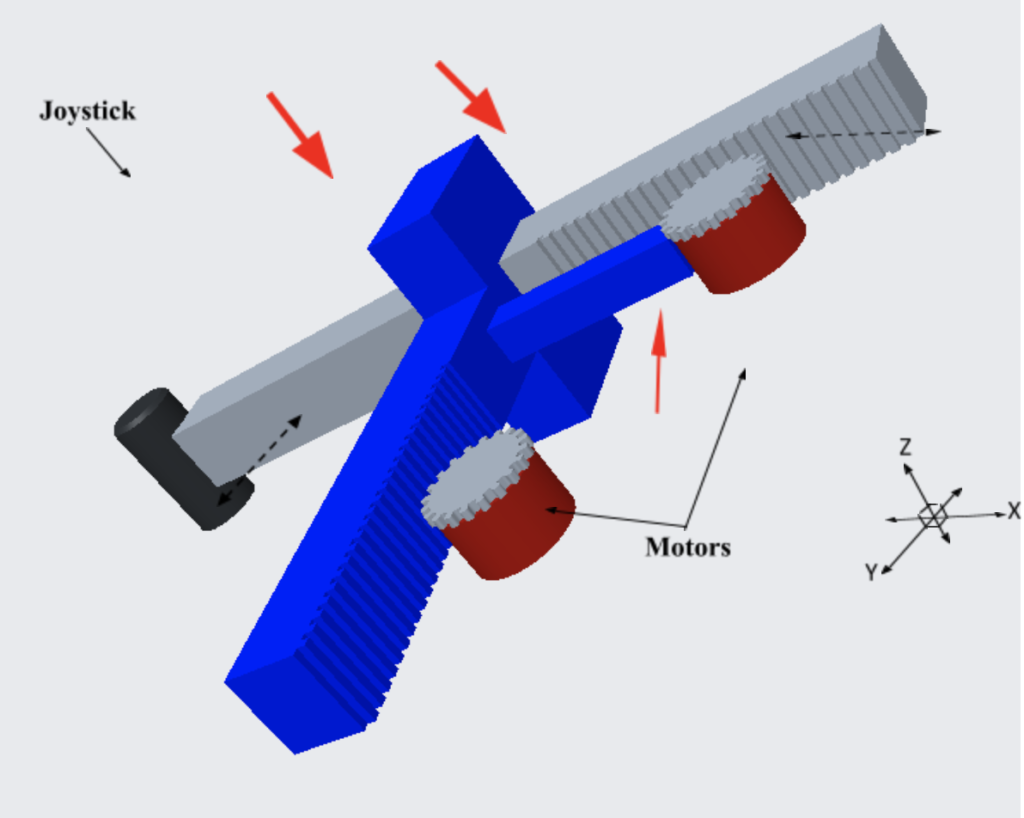
Drawing of the physical apparatus that was chosen for the final design.
Testing and Evaluation
- Stepper motor control- distance test for Bluetooth: the maximum distance for Bluetooth connection is 28-29 feet.
- Bluetooth to motor timing lag test: the lag is around 1.5 seconds
- Ability to stop the chair if the Bluetooth is disconnected or other failures: if the Bluetooth disconnects because of either exceeding the maximum distance or out of power, the motor will know and push the joystick on ATC back to the origin to stop the ATC.
- Bluetooth compatibility with motors (Mobility test): Bluetooth cooperates with motors very well. The only limitation is the time lag mentioned above.
Customer Feedback
We received a positive response from our customer, Will Soles, on the approach we used to allow for remote control of the Action Trackchair. In addition, he liked that our device was removable and could be adjusted to be compatible with different wheelchairs.
Future Steps
- Battery indication circuit – this would allow for an LED to light up when the battery is getting low and signals that the controller need charging.
- Battery consideration for the motors – figure out a component to take power from the wheelchair itself so the motors will never run out of battery.
- Increase speed when moving ATC joystick back to rest.
- Smaller scale of the physical apparatus – the current model was created at a larger scale to ensure design and further models will need to be smaller to fit on the wheelchair better.
- Usage on other wheelchairs – the adjustability of our design for other wheelchairs will still need to be considered.
- Full scale manufacturing – create PCB for cleaner assembly of electronics, create own controller shell for more organization and space.
- Marketing options – dealing with customers one by one or selling to the public as one general product specifically for ATC.
Acknowledgments
THANK YOU to:
Our customer Will Soles for providing our project.
Dr. Amy Lerner and Dr. Scott Seidman for their guidance and feedback.
Art Salo for providing consultations and machining services.
Team Members
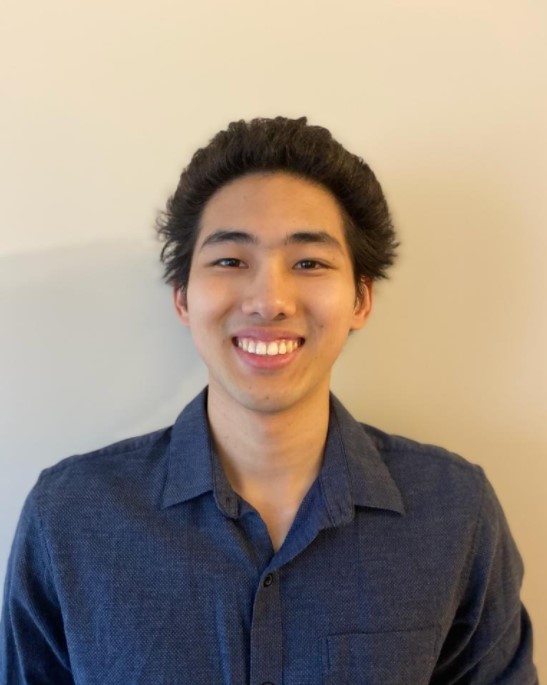
Eric Chang

Yuxin(Ethan) Chen

Meron Abate
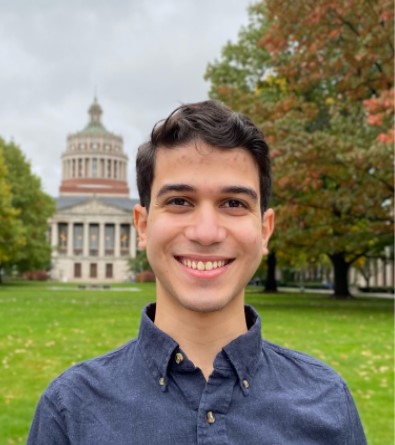
Mohammed Abumuaileq
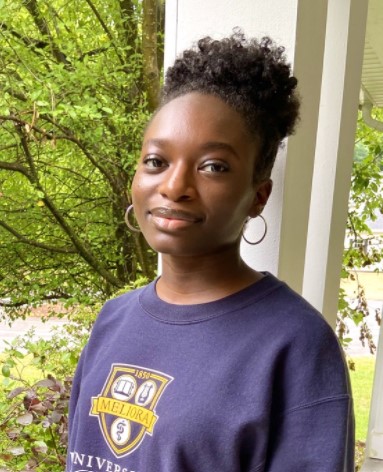
Rebecca Mathurin