Team
- Yiqing Jin
- Samuel O’Connor
- Brent Savage
- Samuel Stoogenke
Customer
Dr. Daniel Brooks – Optimax Systems Inc.
Mentor
Dr. Aaron Bauer – Institute of Optics
Abstract
The goal of this design project was to demonstrate the capabilities of freeform optics in a telescope design suitable for a cube satellite. The desired product is a freeform telescope objective imaging into a spectrometer. The system will be housed within a cube satellite of 6U size, where 1U is 10x10x10 cm.
The system will perform at the diffraction-limit over wavelength range of 400 -1100 nm. The spectrometer will be designed to collect data on the chemical composition of ice sheets, while tracking their growth and movement over time. However, the primary focus of the project will remain on the exploration of designs and showcasing the capabilities of freeform optics.
Freeforms, as classified by most optics manufacturers, are surfaces in which the sag profile lacks translational or rotational symmetry and can be described using Zernike polynomials. For this application, all three mirrors were fitted using the first 37 Fringe Zernike’s in the Code V environment.
Exploration of Solution Spaces
Throughout the design process, our main struggles were 1) Minimizing the astigmatism (Z5) Zernike coefficient, and reducing the freeform departure. 2) Maintaining a diffraction-limited performance while fitting the volume within 2U. 3) Fixing the mid-field distortions and the image plane curvature.
To solve the problems above, in Design A, we controlled the X & Y focal lengths. In Design B, we flipped the X & Y field orientations to minimize spread along Y and tilted the entire system to make full use of the 2U space and loosen volume constraints. In Design C, we switched the stop location from the primary mirror (M1) to the secondary mirror (M2), used real ray constraints for the image curvature, controlled mid-field points distortions, and the value of Zernike coefficients used.
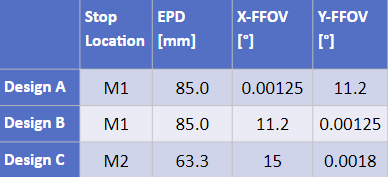
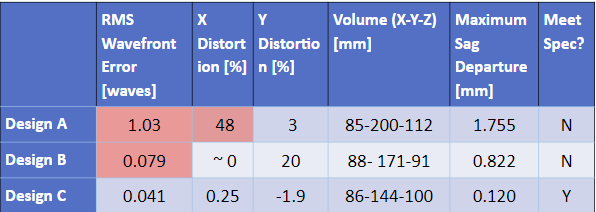
Final Design
he final design form is a F/2.4, three-mirror anastigmat with the aperture stop on the secondary mirror. It has an EPD of 63.3 mm with a FFOV of 15°. The design is diffraction-limited from 400-1100 nm with a max RMS wavefront error of 0.041 waves. The distortion in X is 0.25% and 1.9% in Y.
The objective design fits within the 2U constraint with room to spare for mounting, compensators, electronics, and thermal controls. Its dimensions are 86 mm in X, 144 mm in Y, and 100 mm in Z.
The final design was toleranced to determine ease of assembly. After analysis of our final design with precision tolerances, the diffraction limited yield is ~30%.
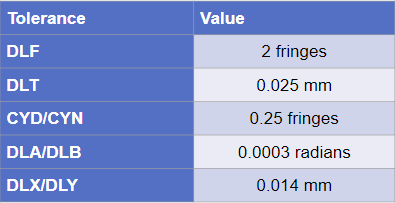
Cube Satellite Layout
A 6U cubesat has dimensions of 100 x 200 x 600 mm to fit our objective, the spectrometer, and all motion controls. We’ve budgeted 2U for motion control, 2U for our objective, and 2U for the spectrometer. Accounting for wall thickness, mounting, and mirror manufacturability, designed our mirrors with a maximum clear aperture of 86 mm.
Freeform Comparison
For comparison, we also designed a non-freeform three-mirror anastigmat using only off-axis conics. Holding volume and distortion the same as in design C, the maximum RMS wavefront error was 36.6 waves. This non- freeform design is about 900 times worse than our freeform performance of 0.041 waves.
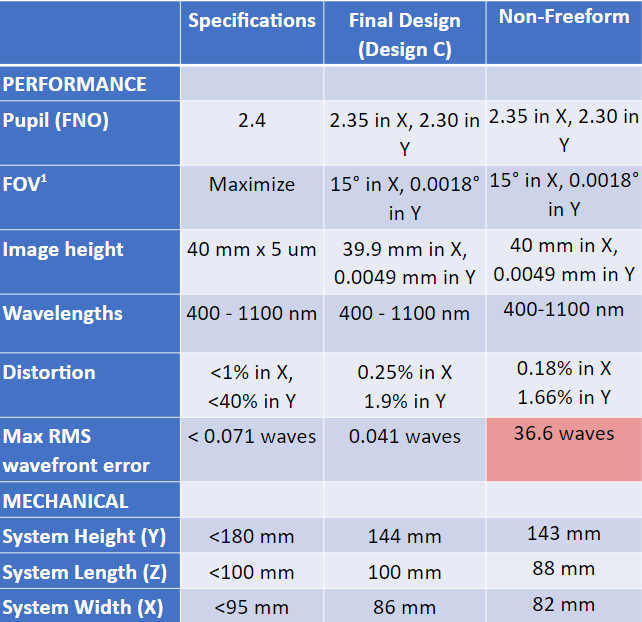
Manufacturability of Freeform Surfaces
In addition to the design of the telescope objective, manufacturability of the freeform mirror surfaces was ensured by analyzing surface sag departures. Sag departures can be described as the deviation in surface figure from a best fit spherical surface. Below are sag departure maps of each mirror as plotted in Zemax OpticStudio, as well as a table of numerical values for the maximum departure of each surface through our different designs. It was determined that maximum departures on the order of hundreds of microns over 40-80 mm full aperture mirrors are well within Optimax’s manufacturing capabilities.
Mirror 1 | Mirror 2 | Mirror 3 | |
Design A | 768 um | 1052 um | 1755 um |
Design B | 221 um | 742 um | 822 um |
Design C | 140 um | 135 um | 120 um |
Conclusion
We were able to design a high-performance, compact, manufacturable telescope objective for a cube satellite imaging spectrometer. A design space for an unobscured, three-mirror anastigmat was explored in order to reach diffraction-limited performance within a 2U footprint while also trying to maximize the objective’s field of view. It was demonstrated that utilizing freeform surfaces in this design form allows for superior optical performance within a tight packing constraint. In addition, the manufacturability of the freeform surfaces and assembly of the objective were thoroughly analyzed. While the final design is still very sensitive to assembly, it was concluded to be an invaluable trade-off for greater optical performance within a smaller overall volume.
Acknowledgements and References
Acknowledgements:
We would like to thank our advisor Dr. Aaron Bauer, who consistently provided crucial design insight throughout this process. Thanks as well to our customer Dr. Dan Brooks for his input and advice, especially regarding freeform manufacturability.
Primary References:
1. Aaron Bauer and Jannick P. Rolland, “Roadmap for the unobscured three-mirror freeform design space,” Opt. Express 29, 26736-26744 (2021).
2. Pantazis Mouroulis, Robert O. Green, “Review of high fidelity imaging spectrometer design for remote sensing,” Opt. Eng. 57(4), 040901 (2018).
3. P. Mouroulis et al., “Snow and water imaging spectrometer,” ESTF (2016).