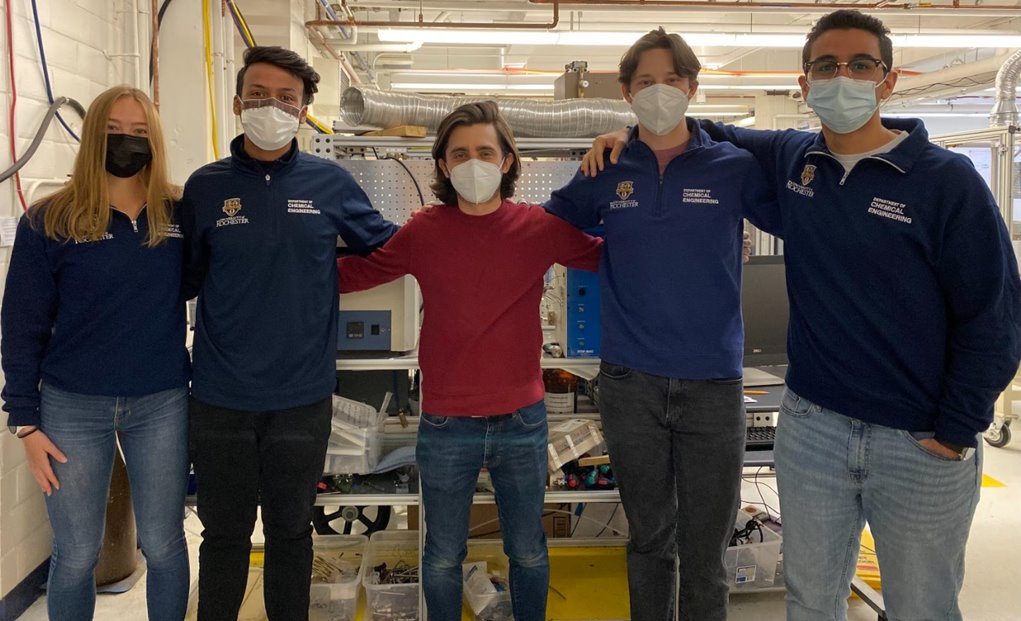
Team
• Kendra Watson
• Kareem Abdelmaqsoud
• Jeremy Rivkin
• Musab Aldosari
Mentor
Marc Porosoff
Abstract
A safe and intuitive packed bed reactor was designed and built for academic experimentation in the Chemical Engineering Senior Lab, CHE 246. Students will have the opportunity to apply fundamental concepts of reaction engineering, thermodynamics, kinetics, and transport phenomena by adjusting parameters and calculating the performance metrics of heterogeneous reactions.
Introduction
The reaction of focus within this system is the reverse water gas shift (RWGS). As shown in Figure (1) and Eq.1, carbon dioxide is converted into carbon monoxide which can be further hydrogenated to useful hydrocarbons through the Fischer–Tropsch process as shown in Eq.2.
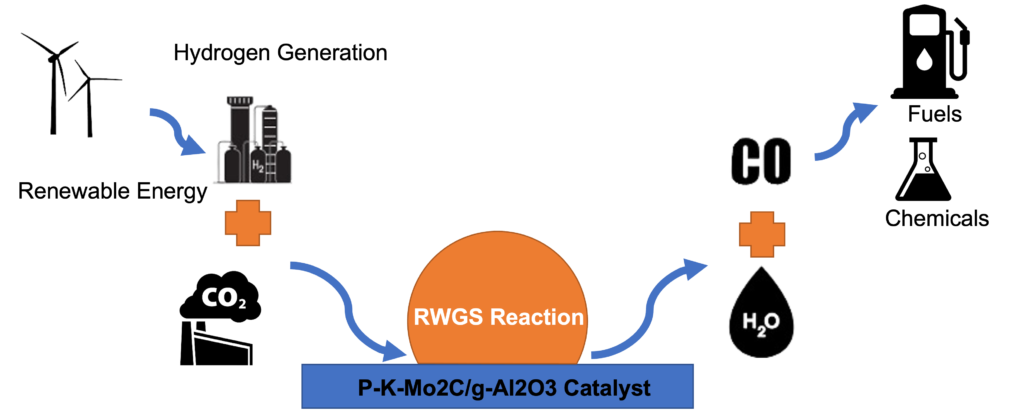
CO2+H2 ⇌ CO+H2O (Eq.1)
ΔG=28618 J/mol , ΔH=41168 J/mol
(2n+1) H2+n CO ⇌ C2nH2n+ 2+n H2O (Eq.2)
The RWGS reaction runs at high temperatures (>600 °C) to achieve high CO conversion and avoid the formationof the undesirable CH4 through the Sabatier reactions described in Eqs 3 and 4. A heterogeneous catalyst of P-K-Mo2C is used to speed up the reaction and obtain the desired selectivity for CO formation under lower temperatures around 450 °C.
CO2+3H2 ⇌ CH4+2H2O (Eq.3)
CO+3H2 ⇌ CH4+H2O (Eq.4)
A heterogeneous catalyst of P-K-Mo2C is used to speed up the reaction and obtain the desired selectivity for CO formation under lower temperatures around 450 °C. A Packed-bed reactor system was built to run this reactor and analyze the product distribution. Figure(2) shows the main components in the system.
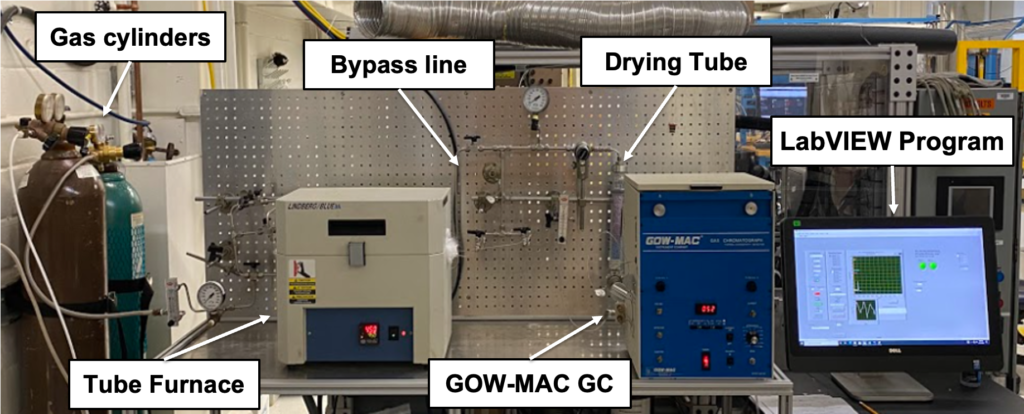
Technical Approach
System performance enhancements included:
• Reducing the number of fittings and connections to reduce potential leak points
• Installing a GC column capable of attaining CO separation
• Increasing H2 and CO2 concentrations in reactant gas cylinder to increase reaction kinetics
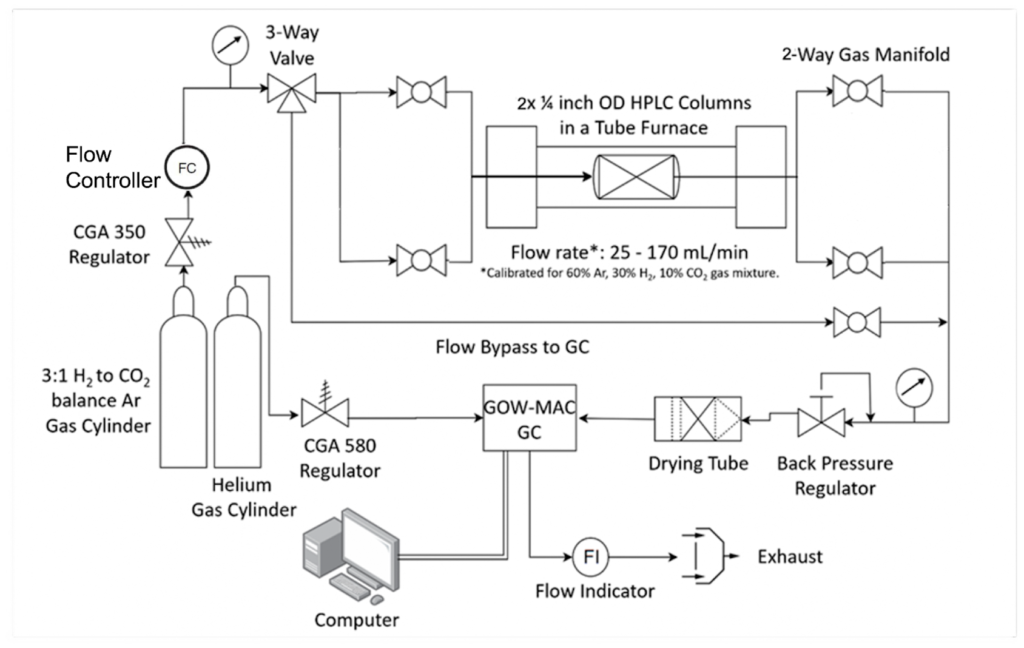
• Fitting the experiment into 3 three-hour sessions
• Developing easy-to-follow SOPs with low maintenance requirements
• Reinforcing student’s understanding of fundamental chemical engineering concepts related to reactor design, kinetics, and thermodynamics
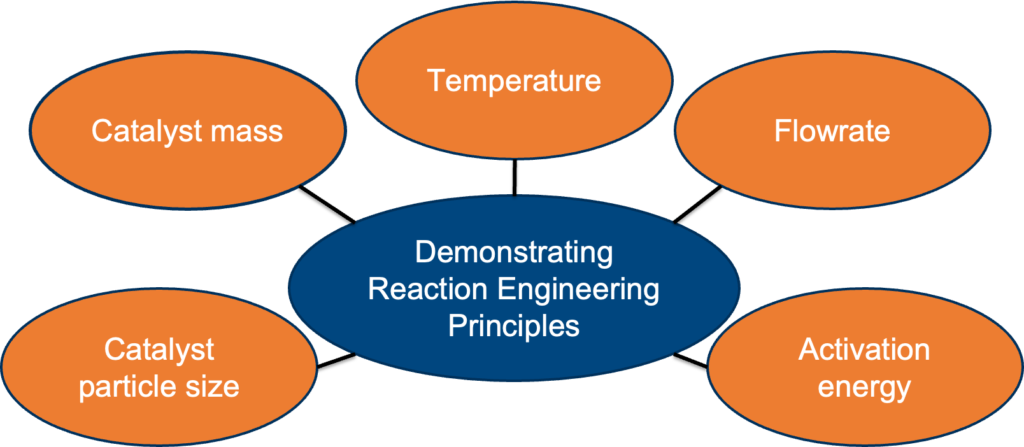
Results & Discussion
As a result of changing the GC column and running many experiments to find the ideal running conditions for the GC, the GC now can separate and analyze all our products. This solves the problem that was faced by last year’s team.
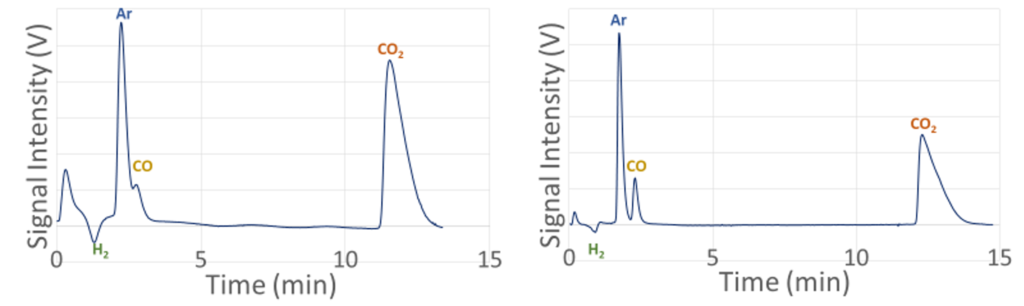
Experimental Design and Execution
• Calibrations between peak area and gas concentration are developed for CO2 and Ar by performing multiple injections with two reactant gas cylinders (10% CO2, 60% Ar, 30% H2; 22% CO2, 12% Ar, 66% H2)
• Changes in CO2 and Ar concentration are used to calculate
• CO conversion as RWGS proceeds
• Conversion and CO concentration are calculated two ways: (1) Assuming volumetric flow rate is constant and (2) assuming inert molar flow rate is constant.
Assumption 1:

Assumption 2:

The graphs below demonstrate a proof of concept for relating experimental data to reaction performance metrics and reaction properties.
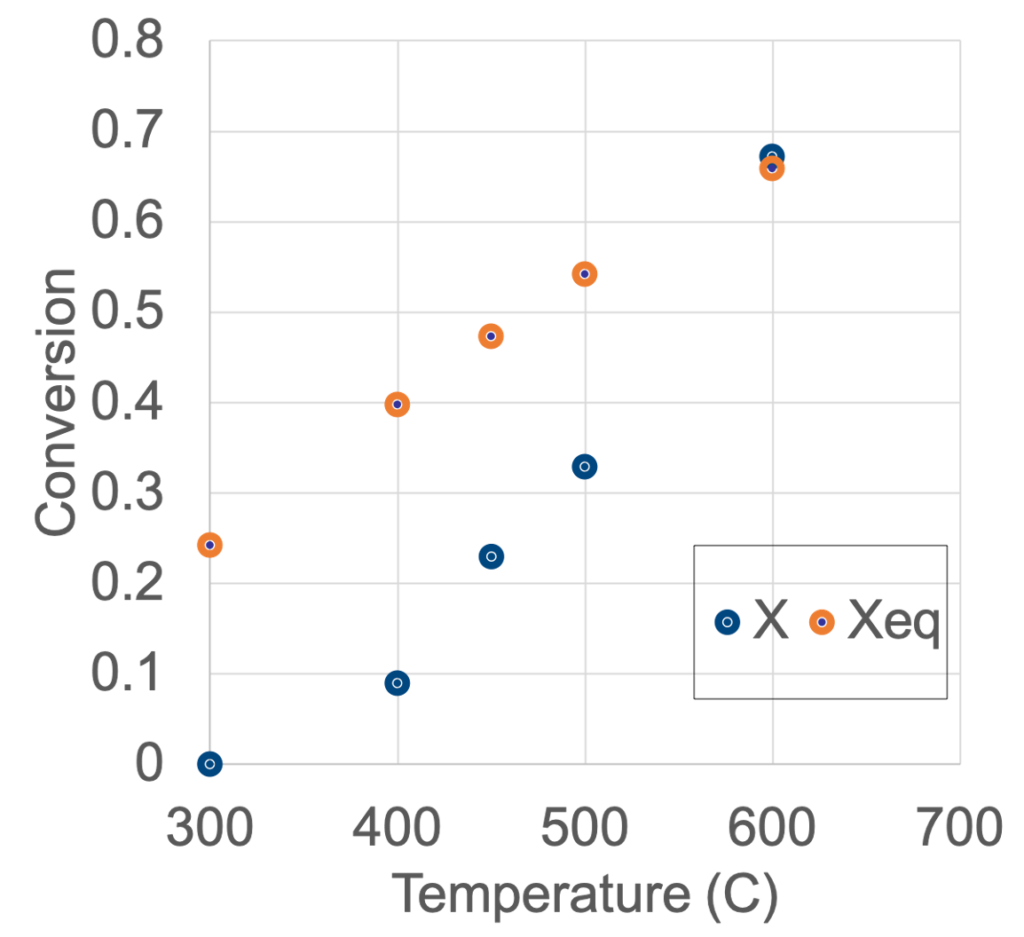
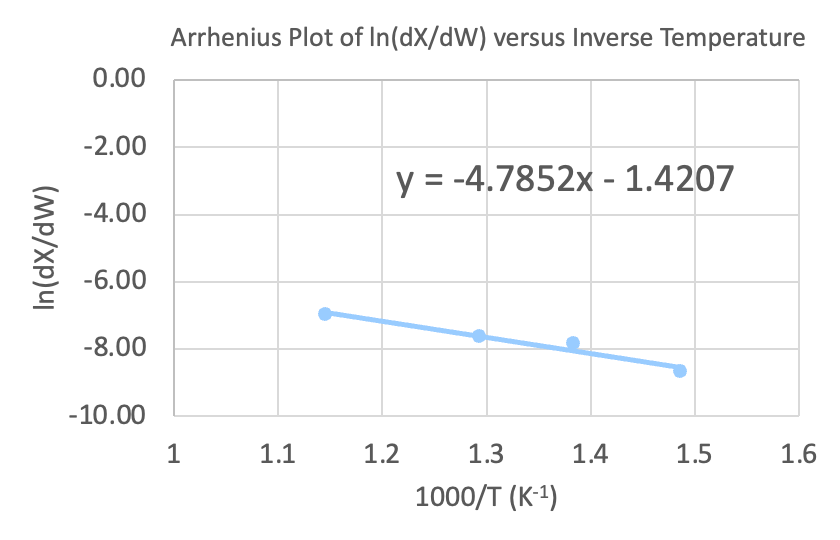
Future Work
• Couple a mass flow controller with a double stage pressure regulator at the reactor system inlet to allow for pressure control above atmospheric without affecting sample injections
• Replacing older connections within the GC
• Reducing start-up time for GC operation from 1 hour and reducing elution time for gas injections to allow for more experimentation within a 3-hour period
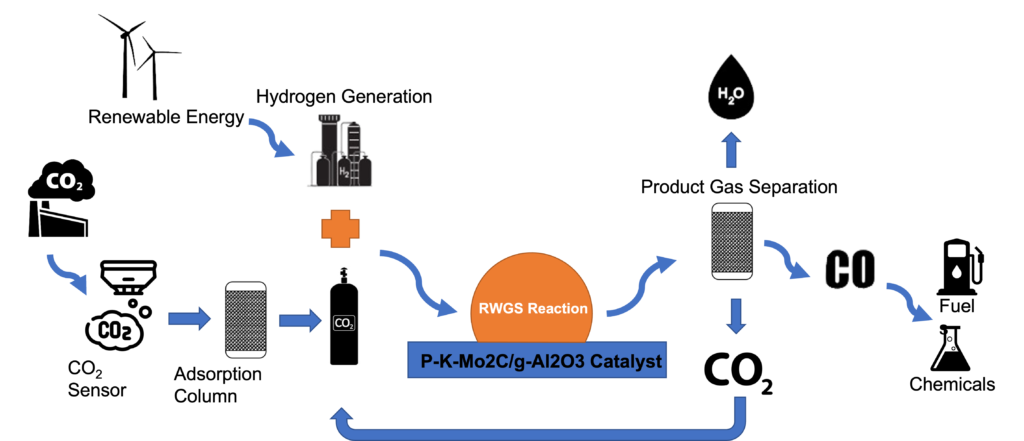
Acknowledgements
Team TTT would like to express its deepest gratitude to the project sponsor,Professor Marc Porosoff. The team expresses its special thanks to the CHE 255 instructors for their availability, support, and feedback. Thank you to Professor Melodie Lawton, Professor F. Doug Kelley, Professor Mark Juba, Clair Cunningham, and Jeff Lefler. We would also like to extend our thanks to Jorge Medina for serving as our project TA.
References
Juneau, M. “Assessing the viability of K-Mo2C for reverse water–gas shift scale-up: molecular to laboratory to pilot scale” Energy & Environmental Science. July 2020. https://pubs.rsc.org/en/content/articlelanding/2020/ee/d0ee01457e
Fogler, H. Scott. Elements of Chemical Reaction Engineering. 6th ed., Pearson Education, 2016.