Lance Ulrich, Greg Schmidt, Evan James, Sarah Fess
The Institute of Optics, University of Rochester
Light sheet microscopy has revolutionized biological imaging by combining rapid acquisition with minimal photodamage. However, calibrating these sophisticated systems requires precision targets that are often commercially expensive and not customized for specific configurations. Our research at the University of Rochester’s Institute of Optics addresses this challenge by developing custom calibration targets using two-photon polymerization (2PP) technology. These targets are specifically designed for our high-NA single-objective light sheet microscope with its unique 42.5° illumination angle. By creating microsphere arrays and sub-micron resolution patterns, we’ve established cost-effective alternatives that maintain high fluorescence properties while achieving positional accuracy within critical tolerances. This project showcases how advanced micro-fabrication techniques can be optimized to overcome significant manufacturing challenges in optical metrology systems.
What is Light Sheet Microcopy
Light sheet microscopy uses a thin plane of light positioned perpendicular to the detection path. This innovative approach enables rapid imaging with minimal photodamage while maintaining high resolution. Our research focuses on developing calibration targets for a high-NA single-objective system inspired by Andrew York’s work. The system’s unique 42.5° illumination angle maximizes both resolution and optical sectioning capability, making designing a custom calibration target to match the bespoke properties of the system extremely useful.
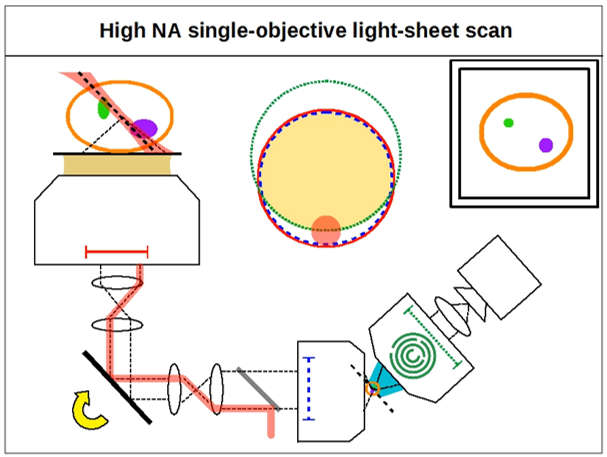
Two Photon Polymerization(2pp)
Two-Photon Polymerization (2PP) enables precise 3D fabrication down to ~200nm feature sizes. The process works by confining polymerization to the focal point of a femtosecond laser, where only the high photon density allows simultaneous absorption of two near-IR photons (780nm) to reach the polymerization threshold. For our calibration targets, we use the Nanoscribe Professional GT system. This advanced platform employs galvo mirrors and piezo stage movements to precisely raster the laser beam through the photoresist material, allowing us to create the complex 3D structures required for our light sheet microscopy calibration targets.

Design Goals:
Our project focuses on developing two distinct types of calibration targets for light sheet microscopy:
Microsphere Targets
We aim to suspend 5μm spheres along the 42.5° angle of our light sheet microscope using high-aspect ratio pillars (up to 100:1). These tall pillars create necessary clearance between the substrate and spheres for unobstructed imaging. Our designed tolerance is within ±400nm, ensuring precise alignment and calibration of the system.
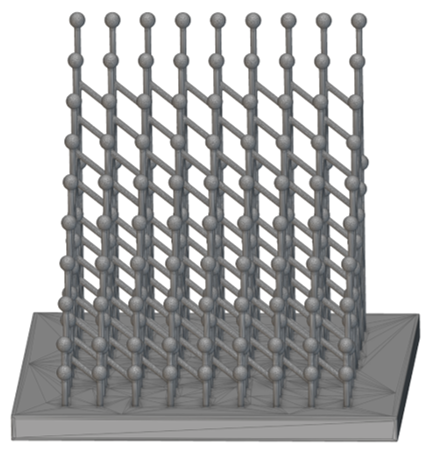
Resolution Targets
To test the resolution capabilities of both our 2PP printer and light sheet microscope, we’ve designed resolution targets with features ranging from 300nm to 1μm. These targets mimic the functionality of one part of an expensive commercial target (using 650nm rings for fluorescence microscope calibration) but at a sibilantly lower cost and with customization for our specific optical configuration.
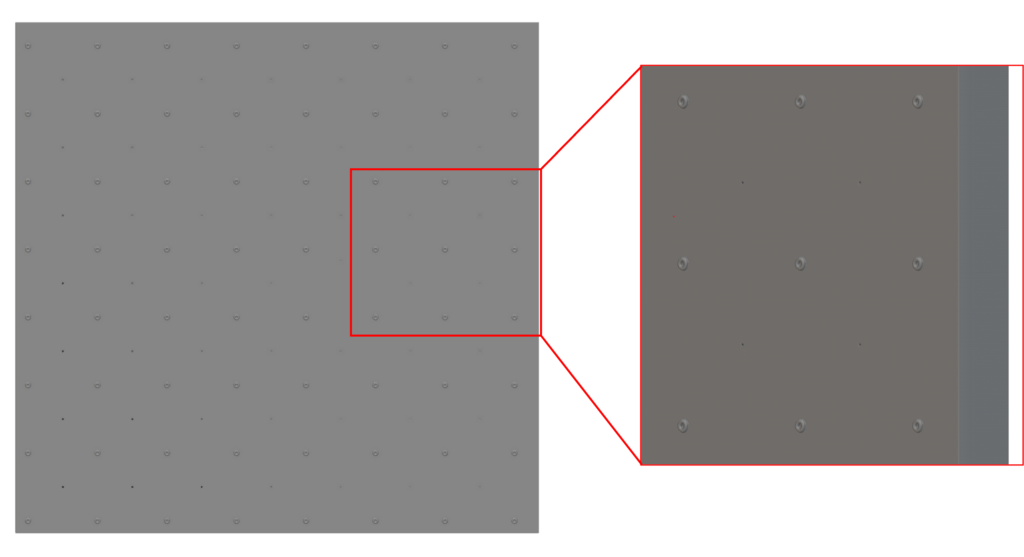
Challenges and development:
Dye degradation
A significant challenge in our fabrication process was the photobleaching of Cy5 dye (647nm excitation wavelength) during extended 2PP printing with the 780nm laser. Photobleached molecules extract during PGMEA development, causing surface roughness and structural deterioration that compromised both physical integrity and optical performance. We implemented a modified solvent protocol to overcome this issue by limiting PGMEA exposure to just 5 minutes and employing extended ethanol development instead. This approach successfully preserved features down to 300nm while maintaining the fluorescence properties and spectral compatibility essential for our calibration targets.
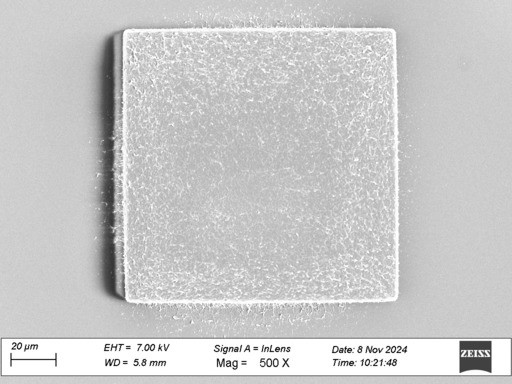
High-Aspect-Ratio Printing
Our initial fabrication results achieved the target sphere diameter tolerance (±0.4μm) but revealed significant challenges with positional accuracy in high-aspect-ratio structures. Severe deformation caused by shrinkage forces and insufficient crosslinking prevented accurate placement at our required 42.5° propagation angle. With a tolerance requirement of just ±0.2° to ensure negligible tilt effects, we needed to implement advanced fabrication strategies.
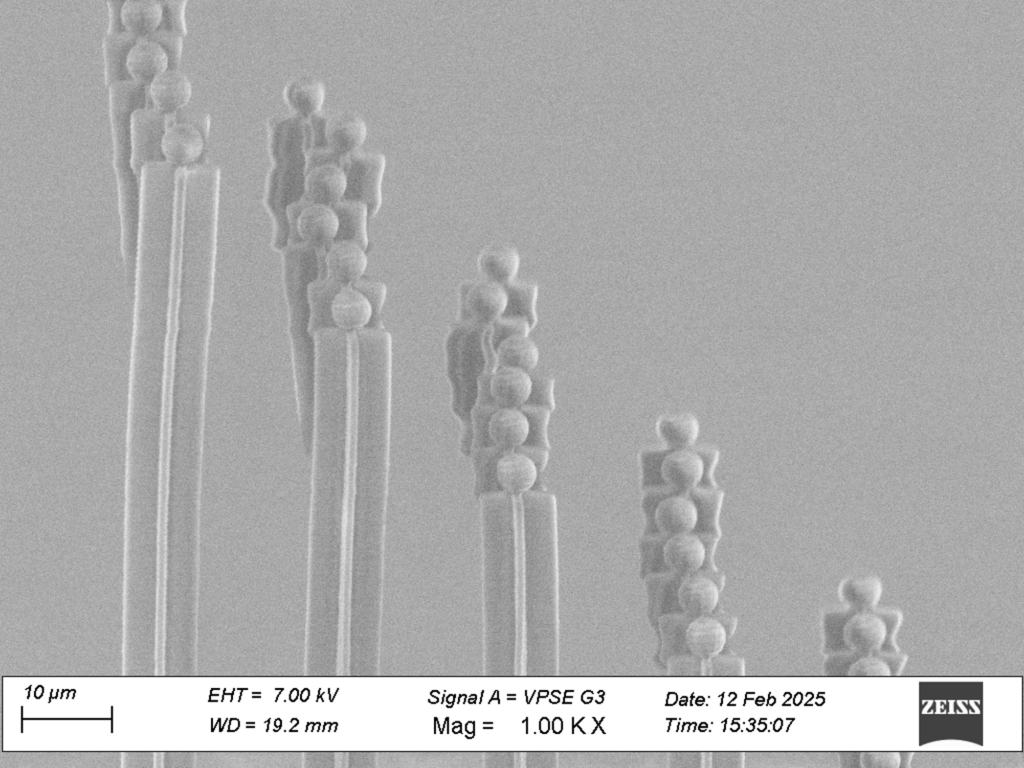
Critical Point Drying Implementation
The extreme aspect ratio of our pillars (~100:1) made them structurally vulnerable during development. Conventional drying processes caused catastrophic collapse due to surface tension forces when transitioning from liquid to gas phase. We solved this problem by implementing CO₂ Critical Point Drying, which eliminates surface tension forces during the development process by avoiding the direct liquid-to-gas transition. This technique preserved structural integrity in pillars exceeding 100:1 aspect ratios.
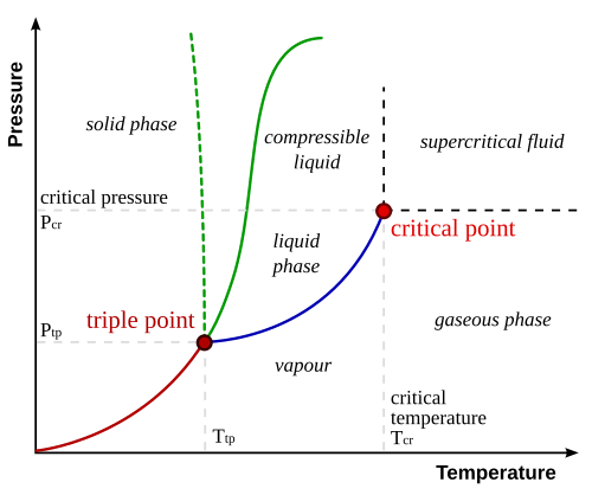
Multi pass printing
Rather than printing line after line in sequential order (traditional approach), we implemented a non-linear multi-pass printing strategy. This technique breaks up the order in which we print each line, creating a non-sequential printing pattern. By distributing the printing process across multiple passes, we can apply more laser power to each line without causing thermal damage or overexposure. This allows for significantly improved crosslinking between polymer chains throughout the entire structure, particularly at critical junctions where structural integrity is essential.
this approach reduced shrinkage by approximately one-third compared to conventional single-pass methods. The enhanced crosslinking density creates more uniform mechanical properties and minimizes internal stresses that typically cause warping in high-aspect-ratio structures. The multi-pass approach was instrumental in bringing our positional accuracy to within ±1μm of design specifications, a critical improvement for maintaining the precise 42.5° angle required by our light sheet microscopy system.
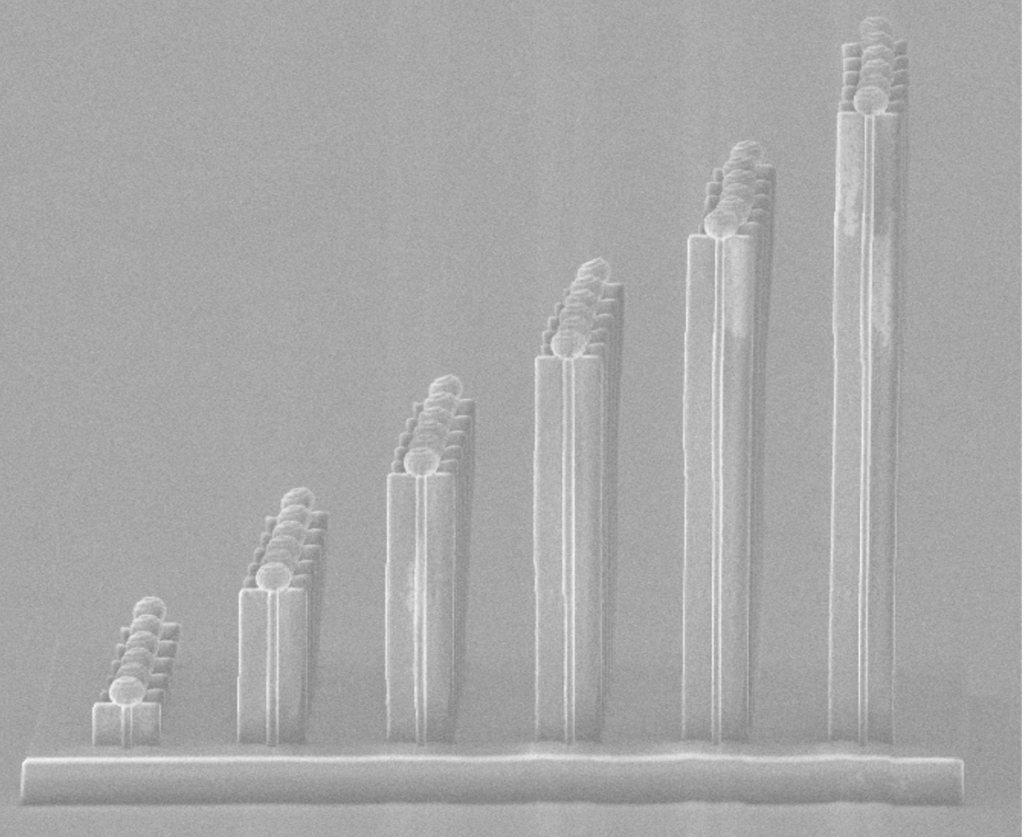
Results
Resolution target
Our ring array successfully demonstrated sub-micron fabrication capabilities with inner diameters ranging from 300nm to 1μm, averaging only 4% smaller than the design specifications. We implemented modified ring geometry to compensate for galvo inertia effects during printing, ensuring consistent feature size. Optical performance testing using Andor Dragonfly confocal imaging confirmed uniform dye distribution, with increased Cy5 and Cy3 concentrations successfully compensating for degradation while maintaining excellent fluorescence properties.
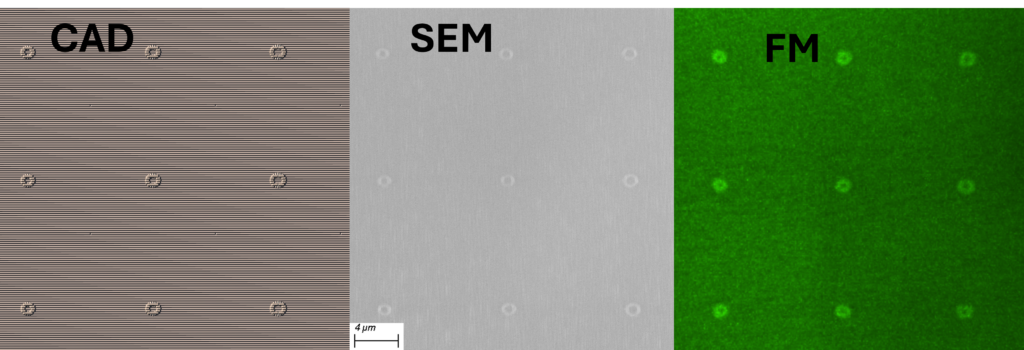
Micro spheres
We successfully demonstrated the 42.5° propagation angle concept with stable high-aspect-ratio features through our combined approach of multi-pass printing and critical point drying. Design compensation was applied to account for remaining shrinkage and deformation. While we’ve made significant progress, our current angle deviation remains at ±0.5° versus our target tolerance of ±0.2° (approximately 0.4μm total deviation across the full structure).
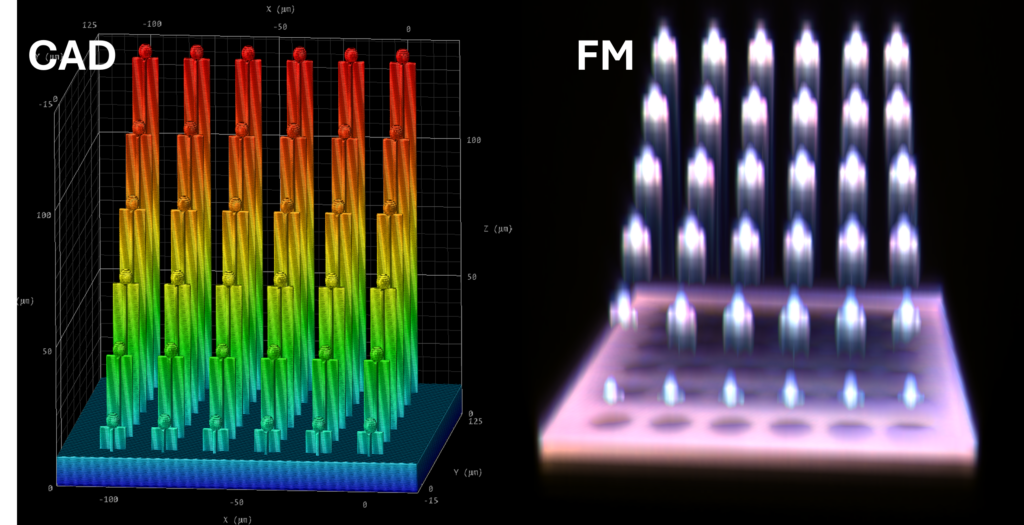
Conclusion & Future Work
Our project has successfully developed two-photon polymerization printed calibration targets with strong fluorescence properties and precise geometries tailored specifically for light sheet microscopy. By implementing modified processing protocols, we’ve preserved sub-micron structures while maintaining spectral compatibility essential for fluorescence applications. These custom targets provide cost-effective alternatives to commercial solutions while offering tailored optical functionality for our specific 42.5° light sheet configuration.
Moving forward, we’ll focus on further reducing pillar warping and improving angle accuracy to precisely match the 42.5° light sheet propagation angle. The next phase will involve testing these targets in actual microscopy workflows to validate their performance in practical applications and quantify the improvement in system calibration.