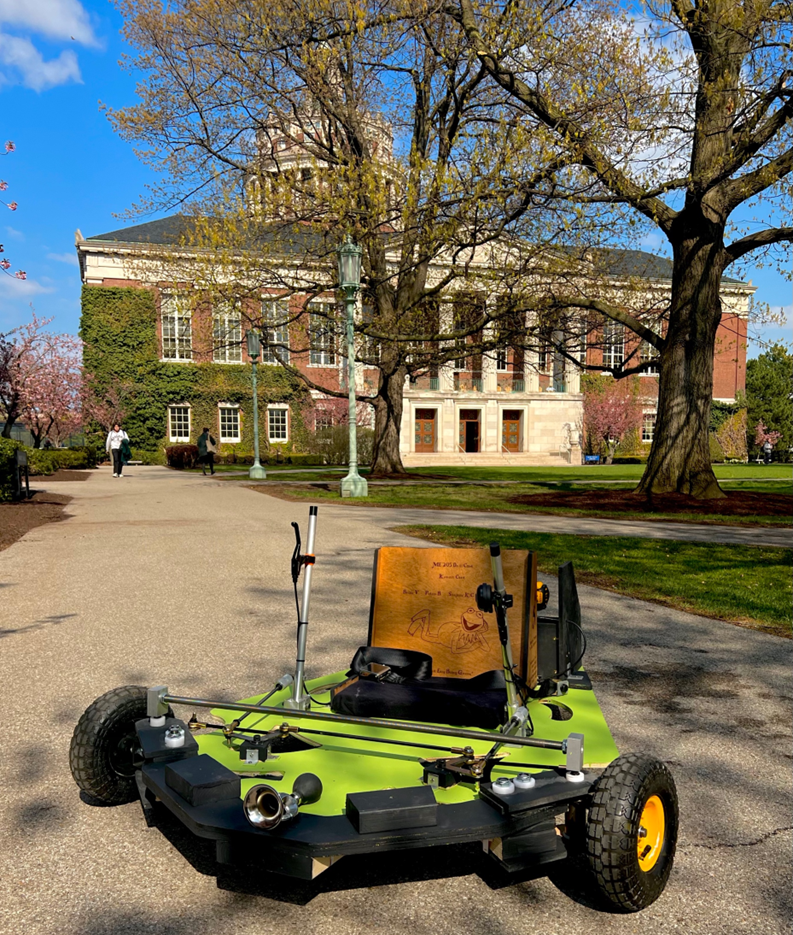
Team Kermit Cart
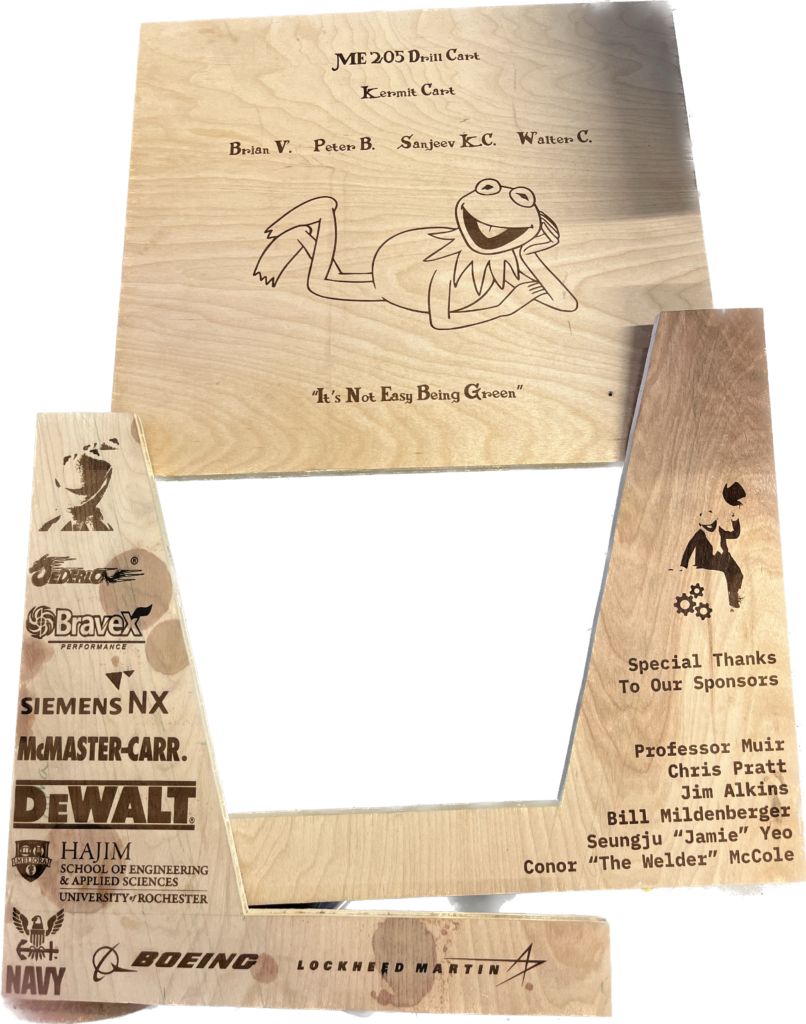
Project Description
The drill-powered cart allows for an alternative, more affordable and accessible option to that of your standard internal combustion engines. Three teams competed, within the requirements and specifications provided below, to optimize a cart to race around the Eastman quadrangle on design day.
Requirements
- The vehicle will be powered by a single electric drill, each team will use the same drill
- The vehicle body will be made from plywood
- The vehicle can be optimized by each individual team
- The vehicle must have a lap style safety belt and horn for safety
- Pinch points must be guarded and pass inspection by Professor Muir
- Payload will be standardized
- Cart must sustain the weight of the driver
- The vehicle must utilize a non-traditional steering system
- The vehicle must be able to maneuver the course
- Each team will use the same wheels
Specifications
- The vehicle cannot exceed 25 mph
- Payloads must be within 5 lbf of each other
- Maximum brake distance of 15 feet at maximum speed
- The vehicle must have more than or less than 4 wheels
- Turn Radius of less than 11 ft.
- Vehicle Dimensions 6ft. x 4ft. x 4ft.
- Cart must travel up a slope of 4.3 degrees
Deliverables
- Drill cart operational on design day ready to race
- Technical report including test results
- Project presentation/website
Concept Selection
Frame: A flexural test was conducted to collect data on the deflection of the plywood sheet under a known load in a 3-point bend configuration.
Steering: Incorporating an Ackermann steering linkage was the most important aspect in the design process for steering the kart.
Drivetrain: The team selected a one rear-wheel drive and two front-wheel steering cart design based on criteria of complexity, maneuvering, and assembly, and designed a chain system to connect the drill on drive shaft to the rear shaft supporting rear wheel.
Usability: The team decided on a mechanical disc brake for the braking system, with a handle braking system that requires 9 lbf to come to a hard stop and incorporated braking handles into the steering mechanism for driver convenience.
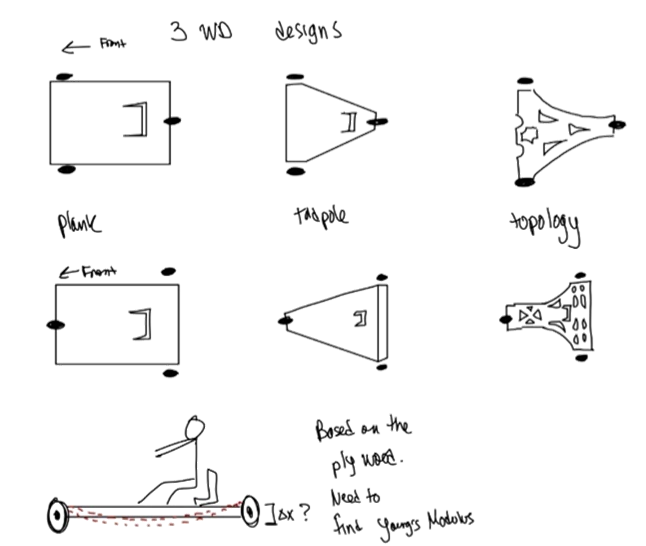
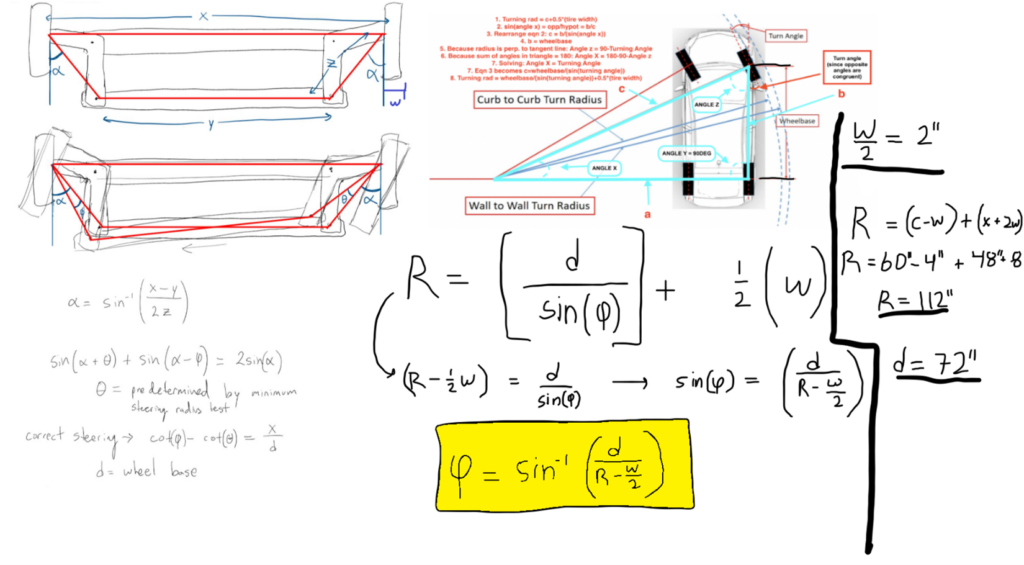
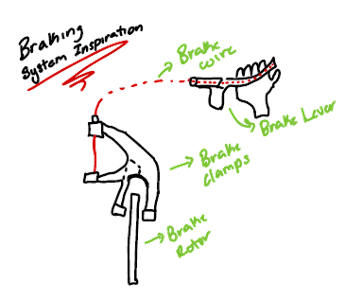
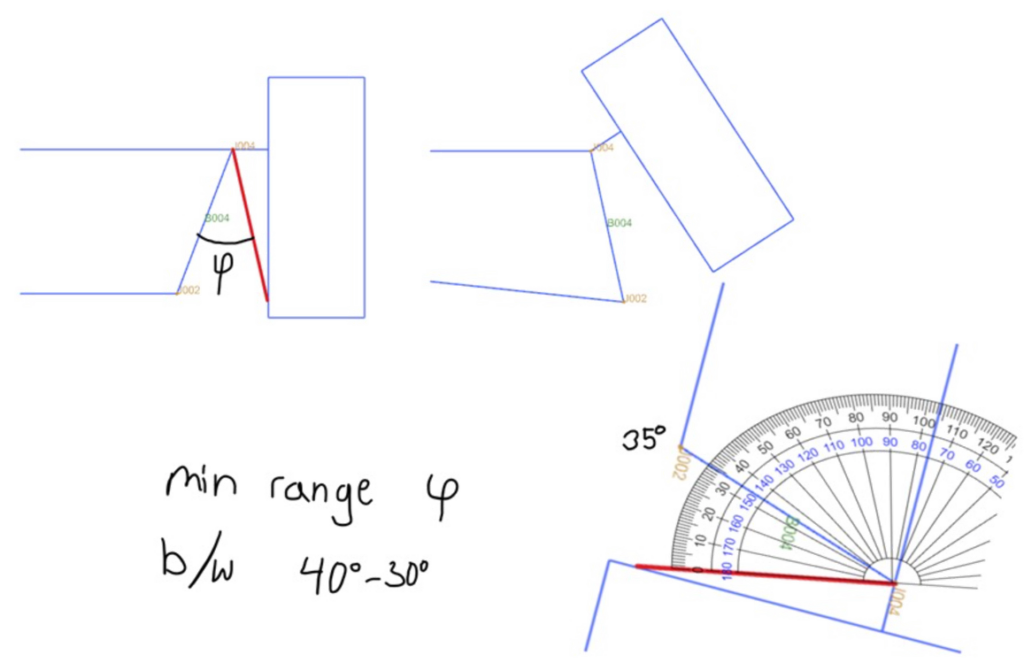
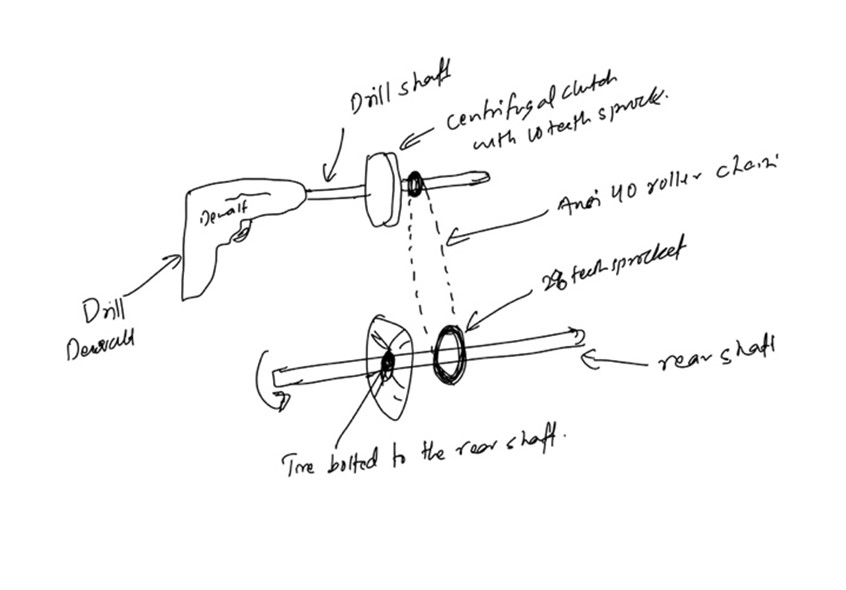
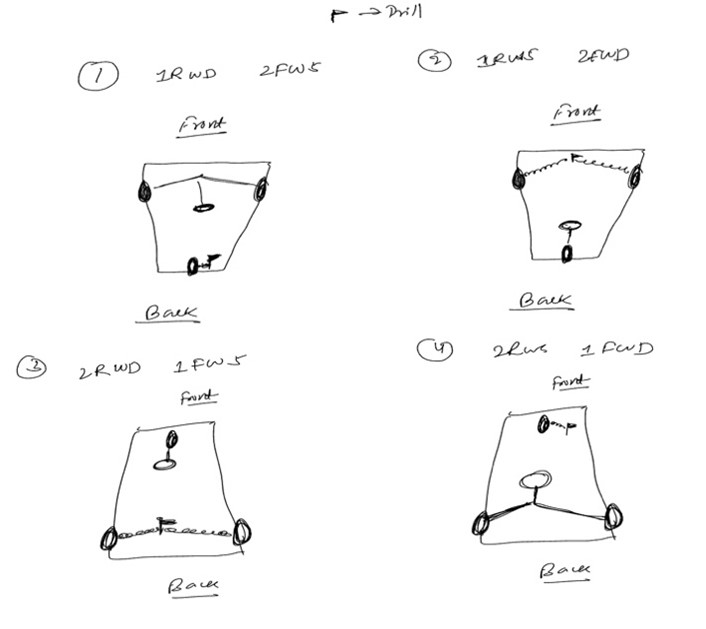
Analysis & Simulation
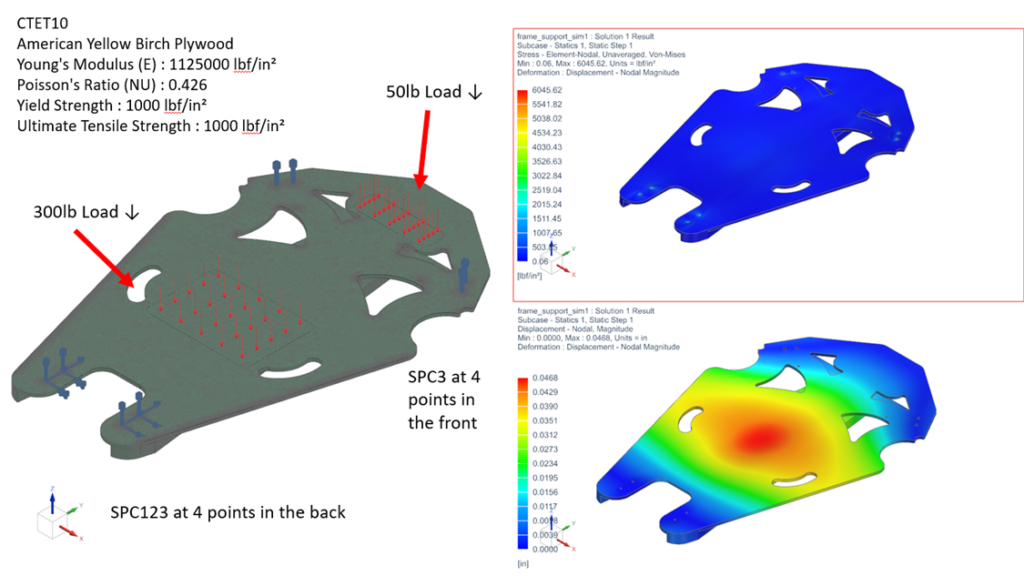
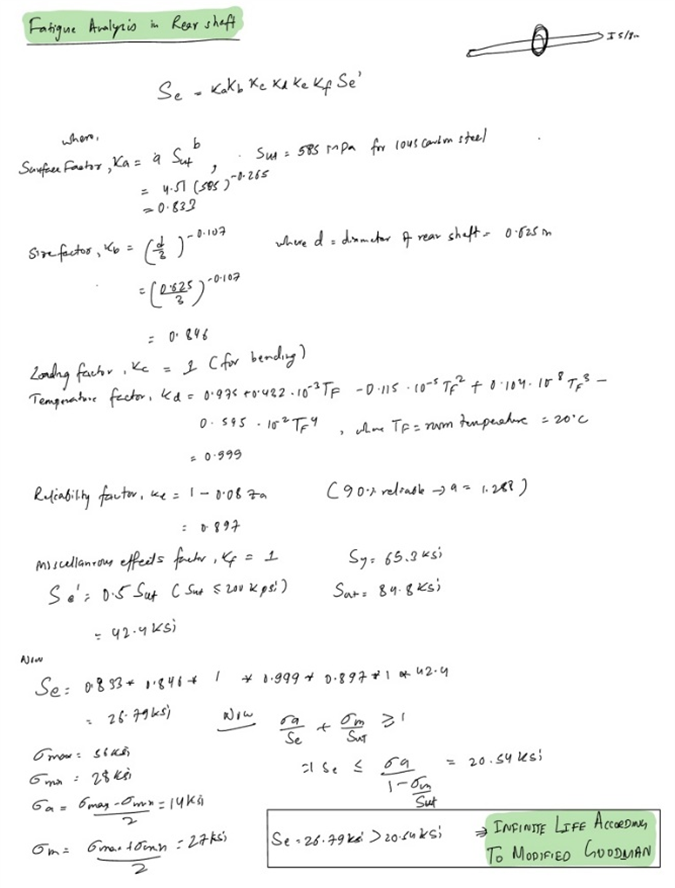
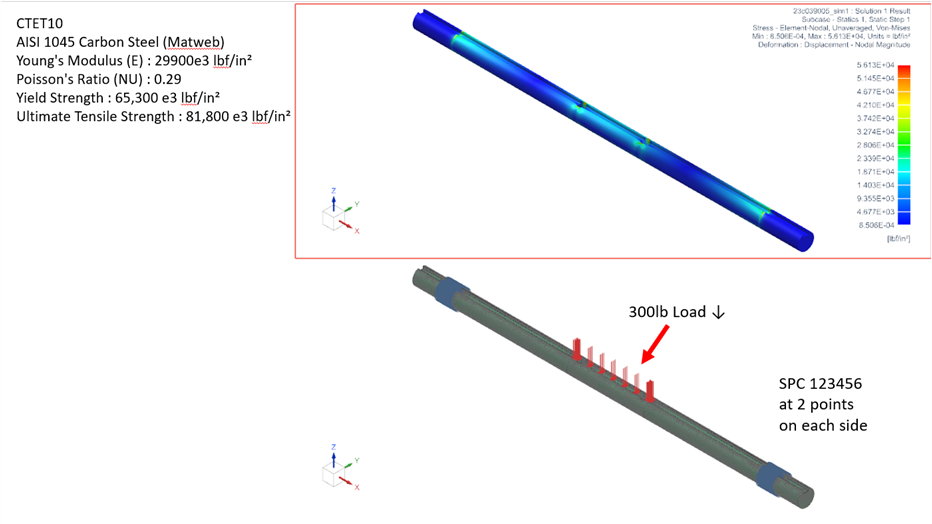
Manufacturing
Description
Frame:
Improved frame support was achieved through 2nd iteration using 2×4 wood planks in a triangular configuration under the car, with a plywood piece under the drivetrain system to prevent screws from ripping out of L-brackets.
Steering:
Steel material was selected for steering knuckle due to weight and moment considerations. AISI 4340 low carbon steel sheet and tube were cut using plasma and horizontal band saw, TIG welded after deburring and bending, and preload bar supports were made from scrap aluminum.
Drivetrain:
Aluminum 6061 and Carbon Steel was used for drill and rear shaft respectively to support one-third of cart weight with driver and transmit torque. Centrifugal clutch engagement was lowered to 100 rpm by removing spring to engage the gears at right speed and avoid the stalling.
Usability:
Parts made of aluminum 6061, manufactured with mill and lathe, including caliper mounting system, handle tubes, and adapter pieces.Adapter mounts were 3D printed to fit the acceleration and braking handles to the steering tubes.
Purchased Hardware | $997.83 |
Manufacture Time ($100/hr) | $17300.00 |
Total | $18297.83 |
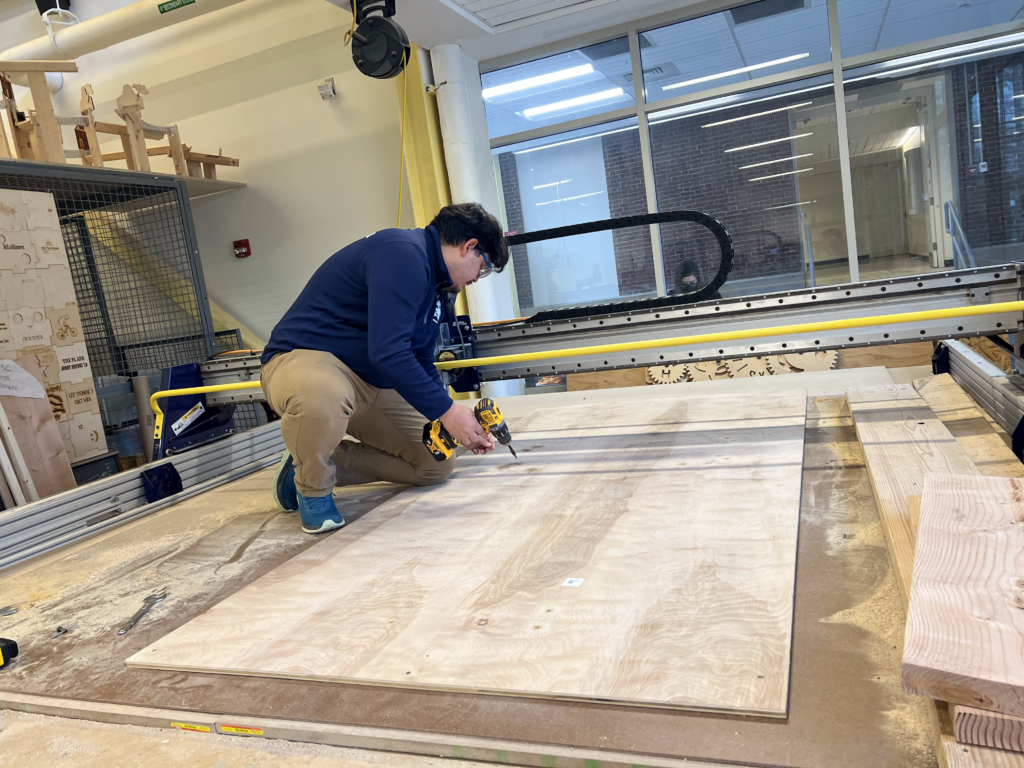
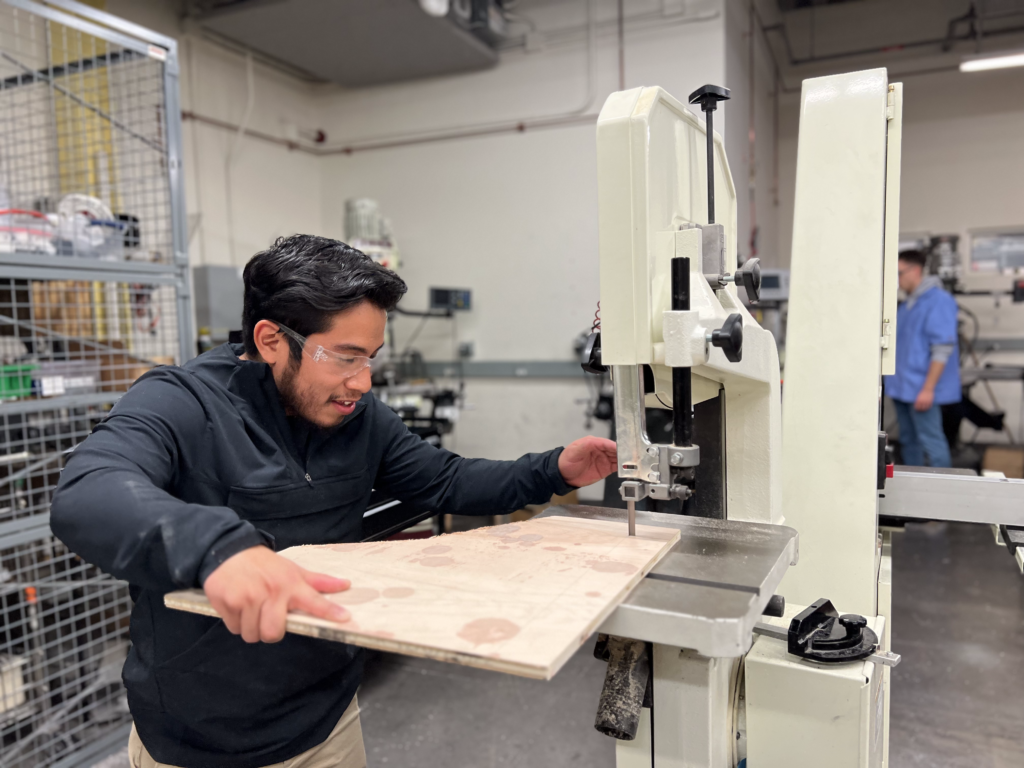
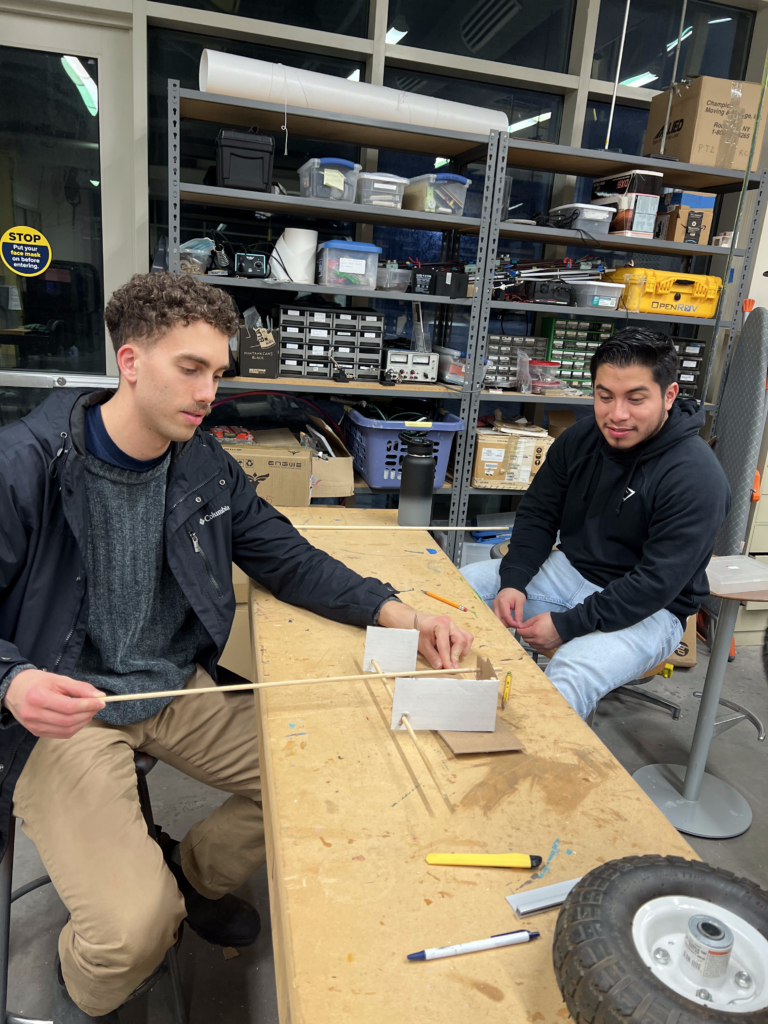
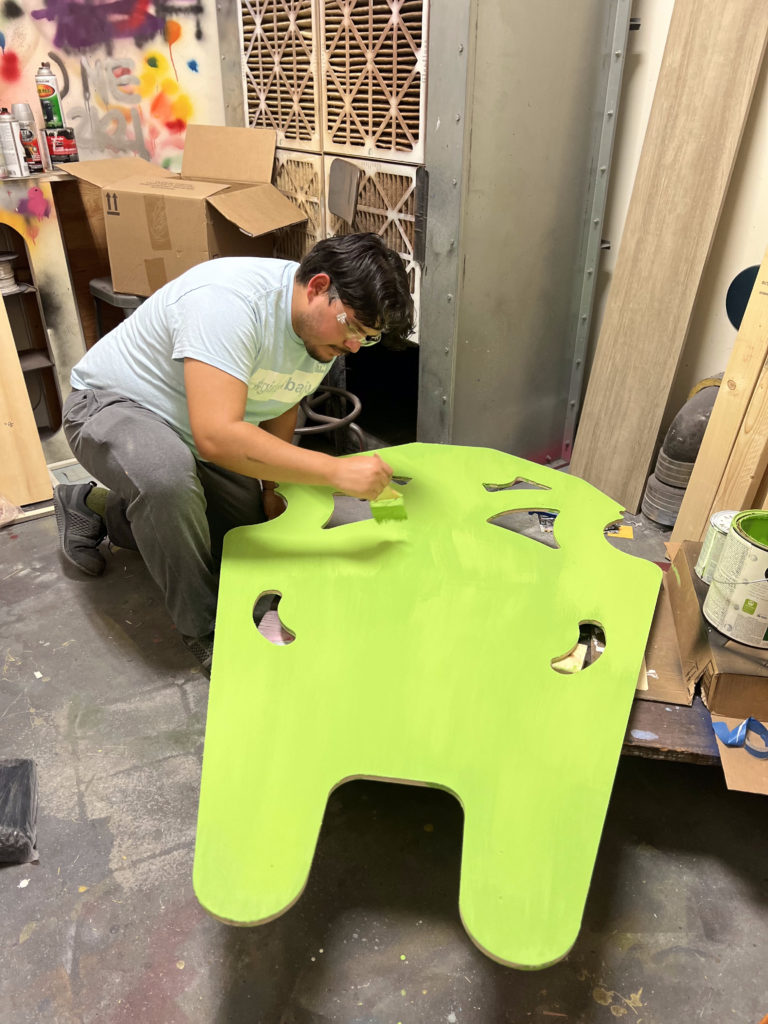
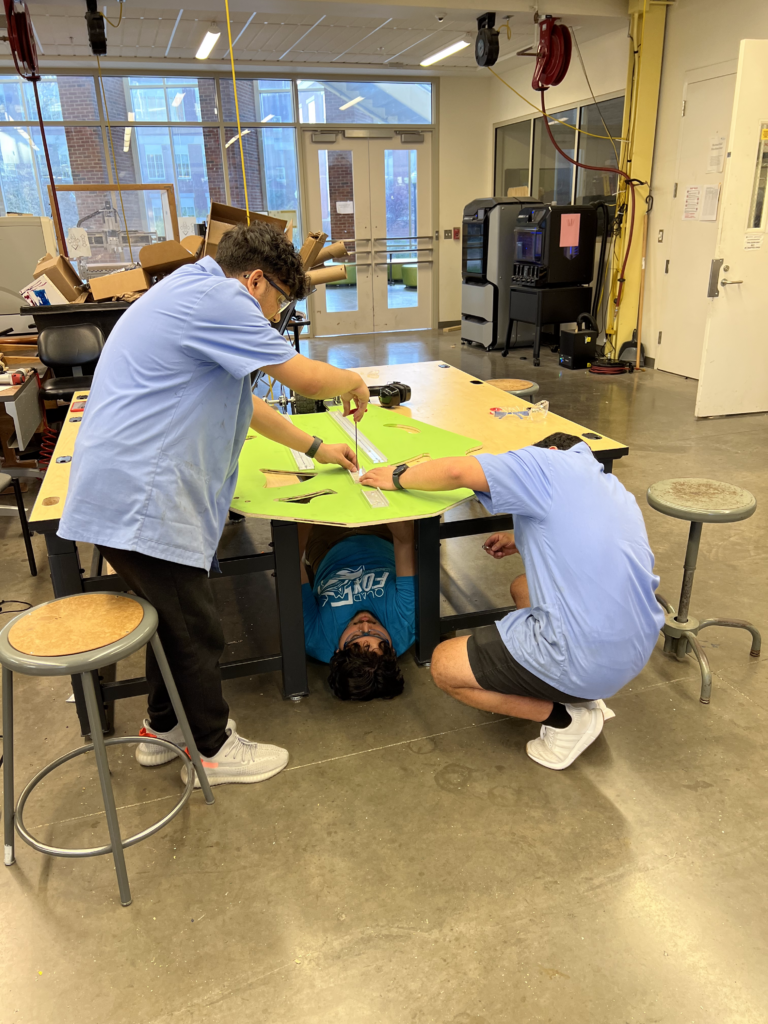
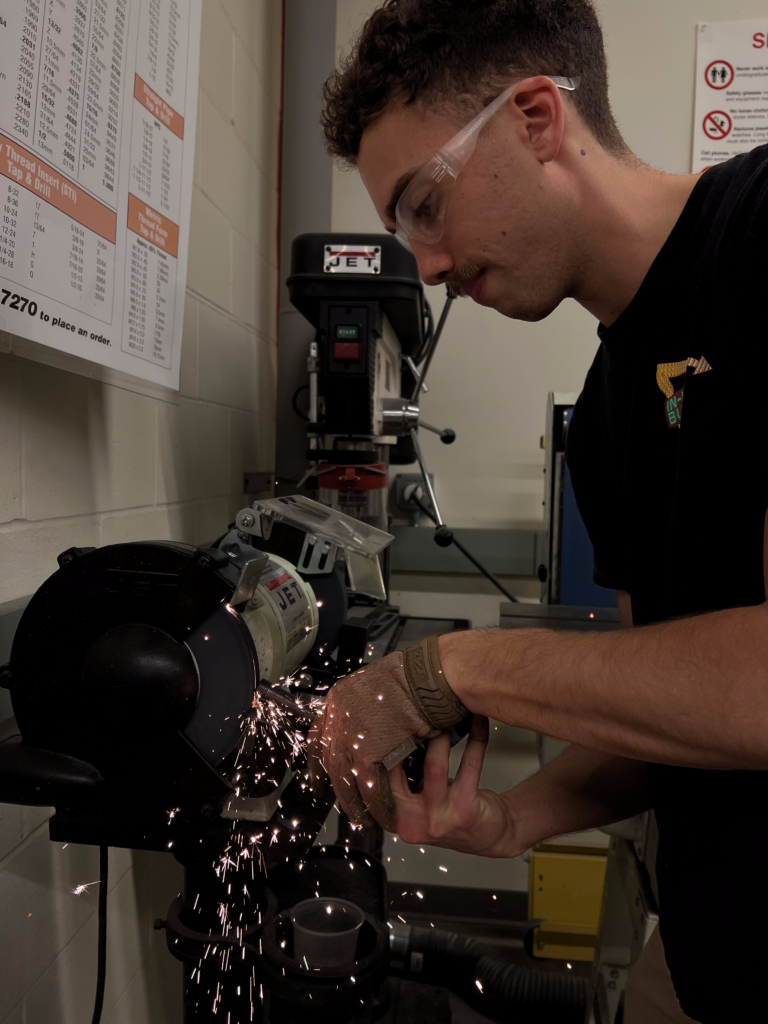
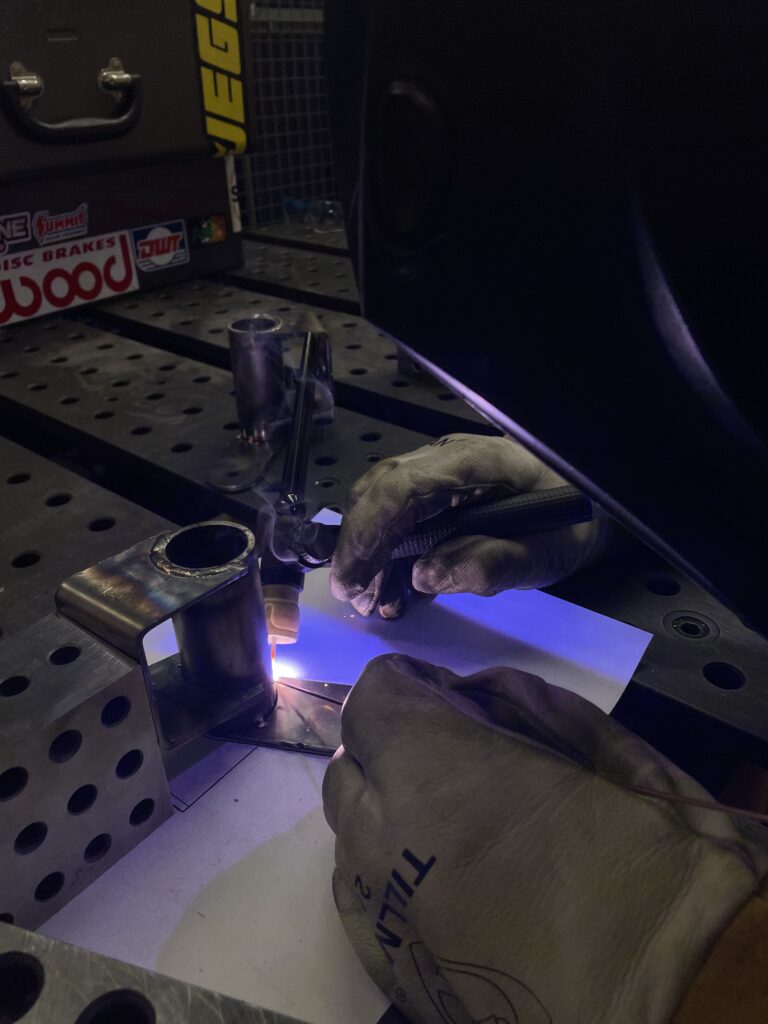
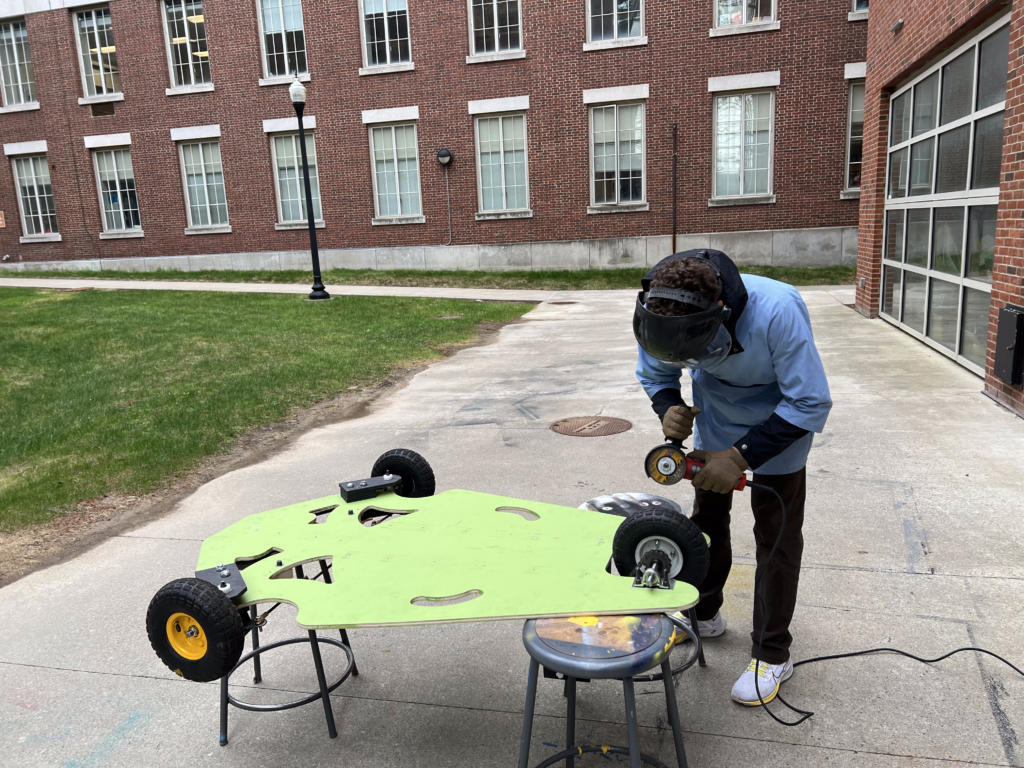
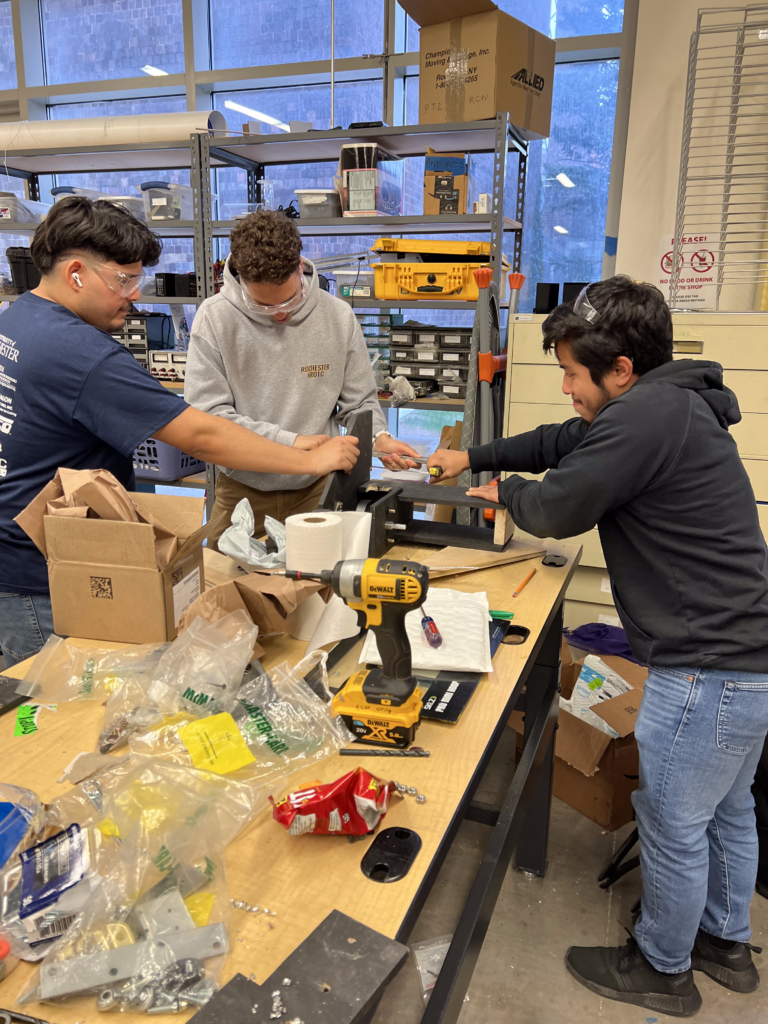
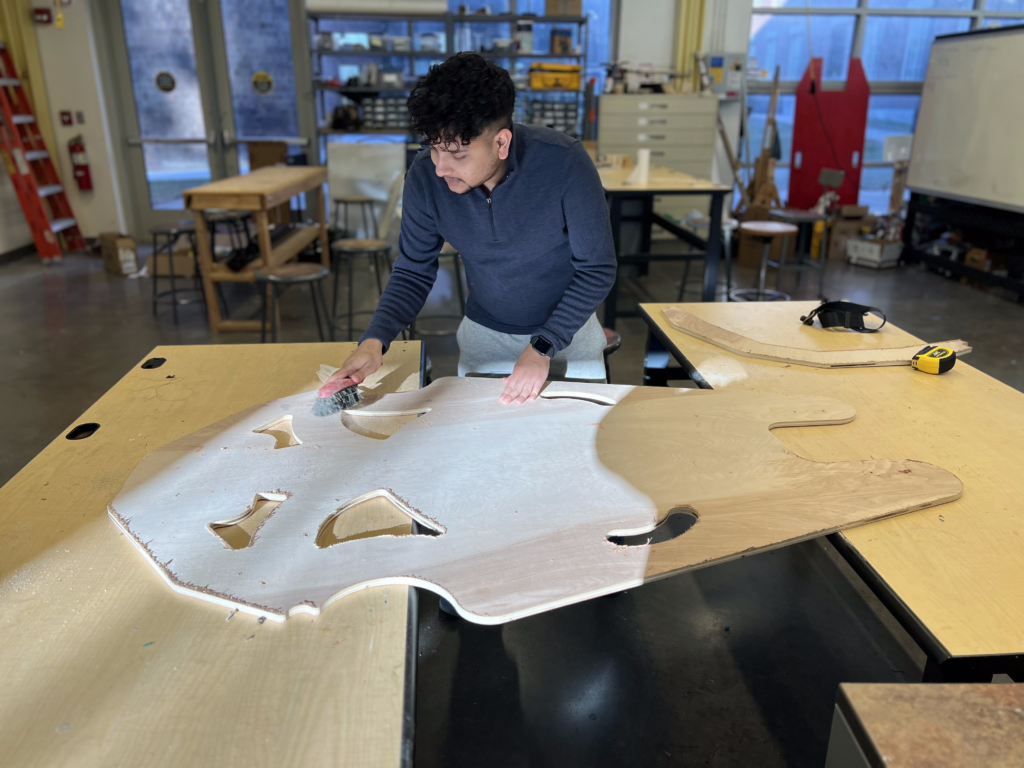
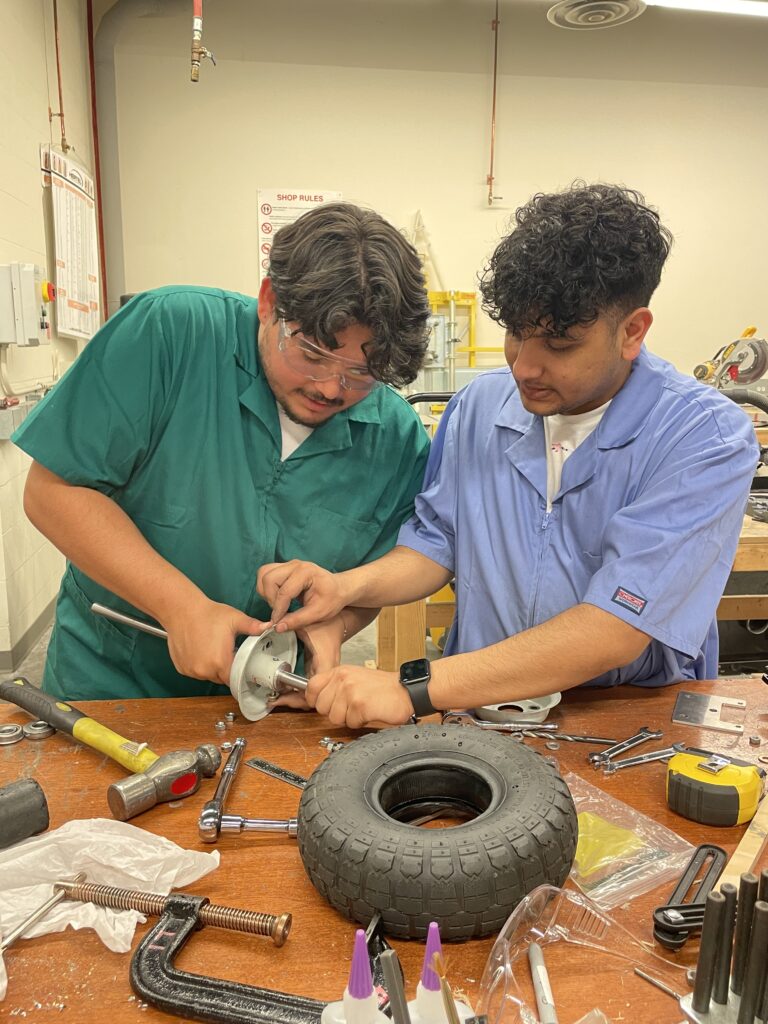
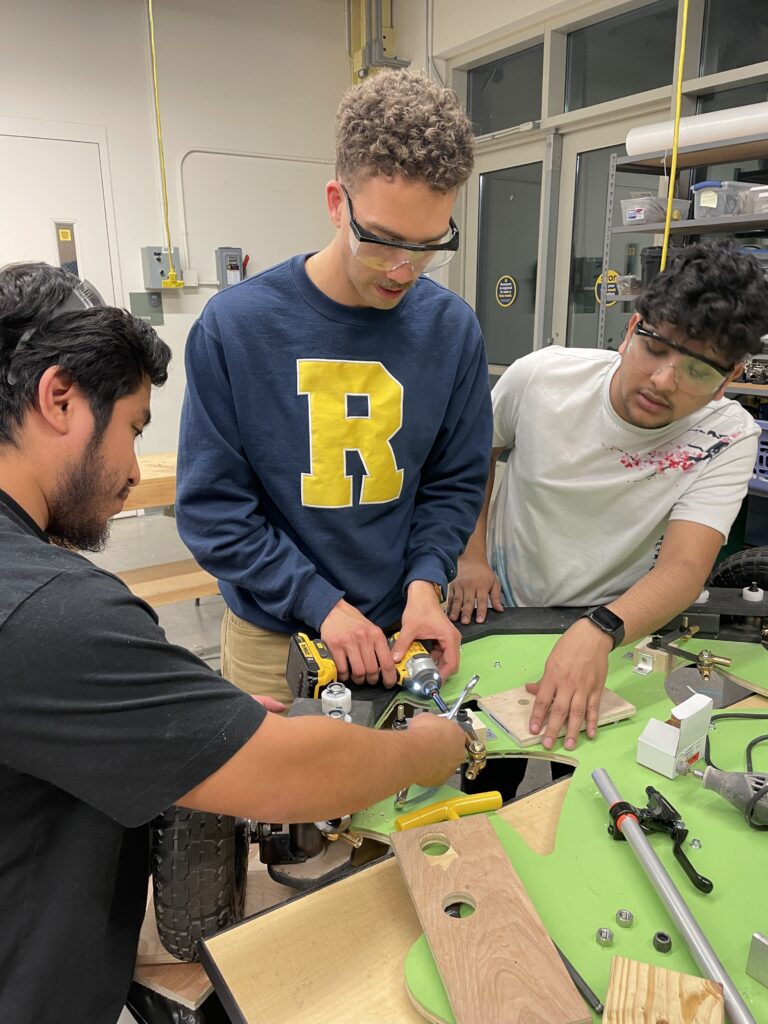
Drawing Package
Testing
Specifications Tests | Results (Pass/Fail) |
Maximum speed <25mph | Pass |
Turning radius <11ft | Pass |
Payload within 5lbf | Pass |
Maximum braking distance <15ft | Pass |
Number of wheels (not 4) | Pass |
Ramp test | Pass |
Vehicle dimensions | Pass |
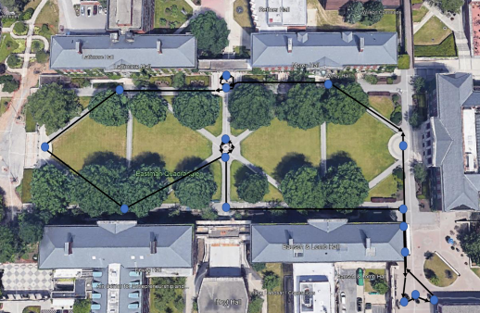
Societal & Environmental Implications
Description
- The drill-powered cart has positive health and environmental impacts by encouraging the use of a rechargeable alternative to gas-powered vehicles and reducing material waste.
- The cost-effectiveness of the cart makes it a potential solution for developing countries and communities with limited resources.
- While there may be limitations such as load capacity and being a one-person cart, optimizing the design can address safety, ethical, and environmental concerns.
- “It’s not easy being green” -Kermit the Frog
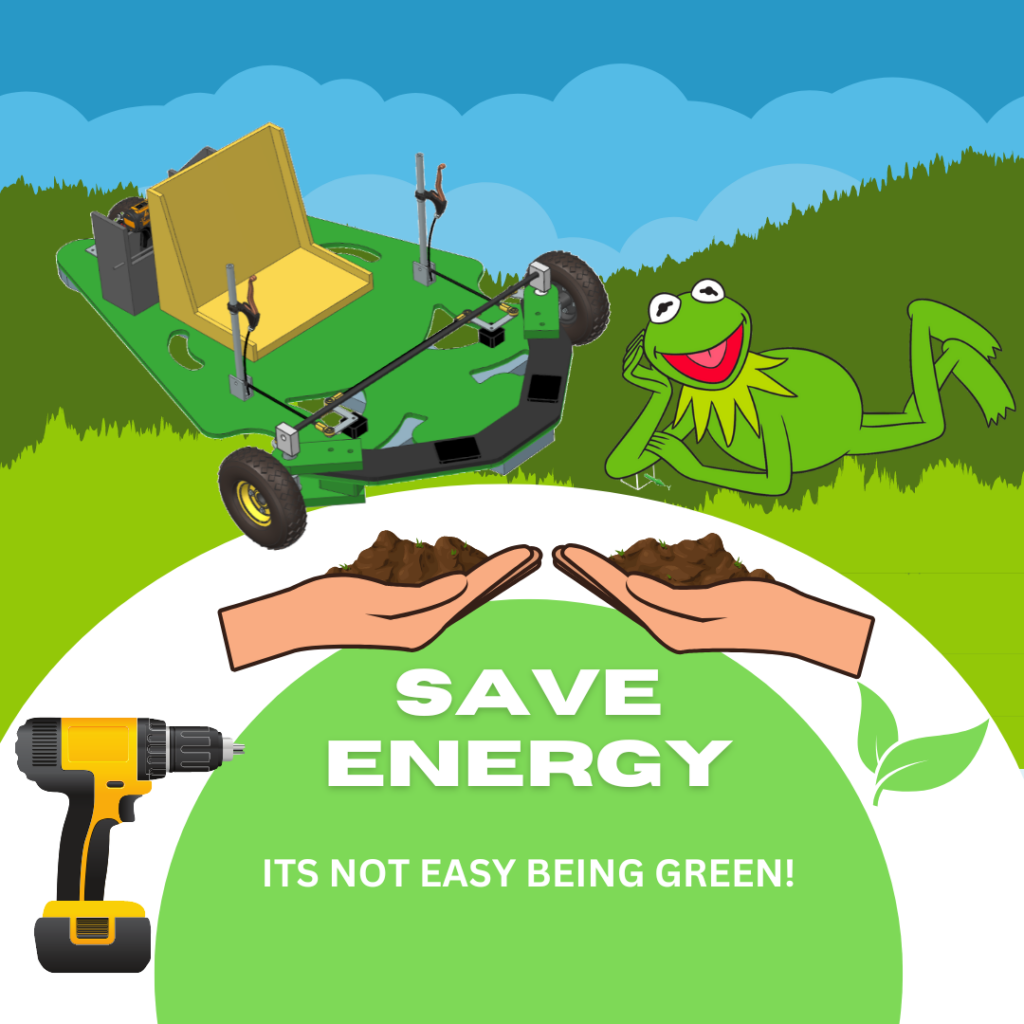
Videos
Final Presentation
Final Design Report
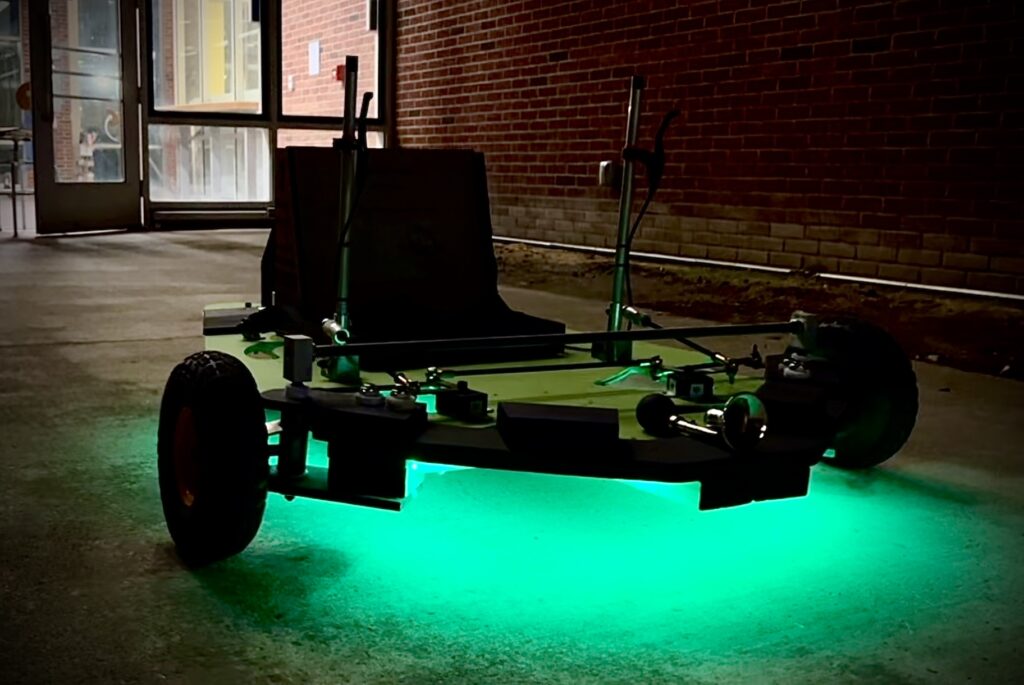
Acknowledgements
We would like to acknowledge the project manager Christopher Muir for this opportunity, Chris Pratt, Jim Alkins, Peter Miklavčič, Bill Mildenberger, Conor McCole and our TA, Seungju Yeo for their assistance in the shop and their support answering questions.
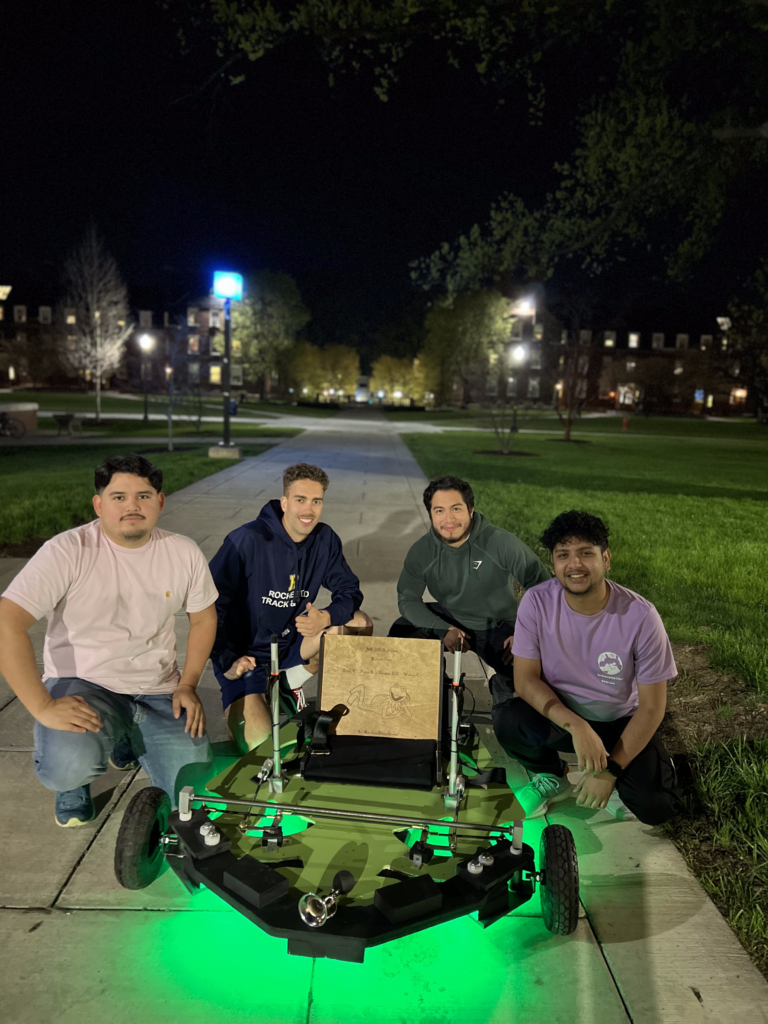