Abstract/Introduction
Getting around campus effectively is a daily struggle at the University of Rochester. This project aims to create a drill powered vehicle to navigate campus which is an affordable, efficient, and convenient solution. The best vehicle will be determined by an endurance race with a Monte Carlo start to determine a winner among the other competing teams. The cart is divided into five different subsystems: drivetrain, brakes, frame, steering, and usability. Each of the five team members were responsible for a specific subsystem.
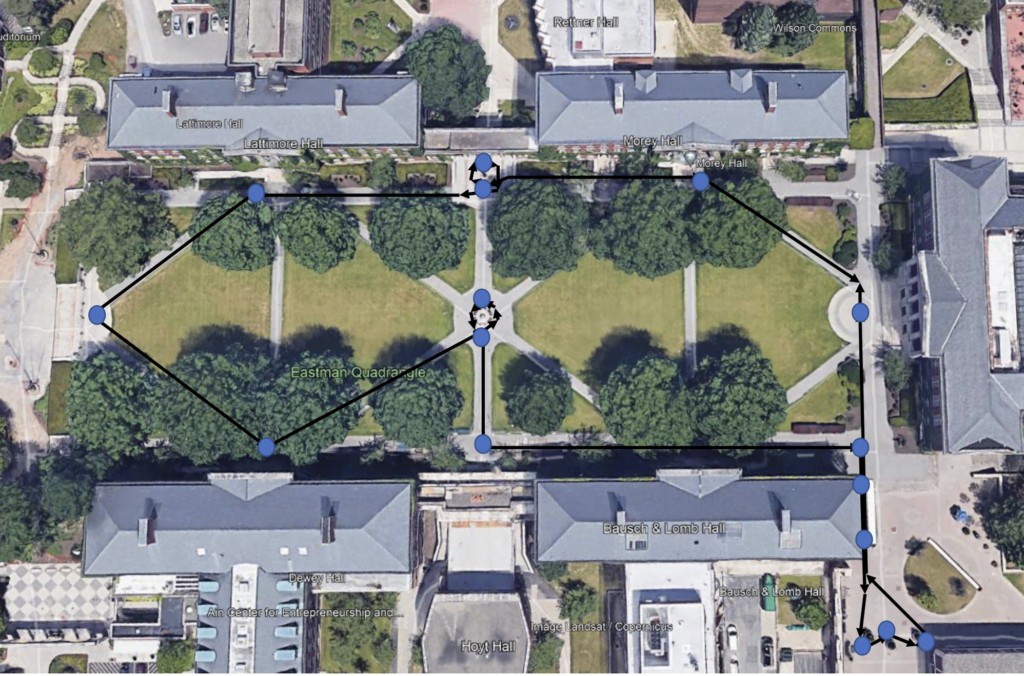
About our Team
- Noah Braid: subsection frame
- Braydon Bush: subsection breaks
- Ryan Eamer: subsection usability
- Caiden Larsen: subsection drive train
- Nicole Mercer: subsection steering
Subsection Analysis
Frame: To adhere to the requirements of the project, the vehicle body must be made from plywood. The plywood body proved difficult to yield under the given use case, and it was therefore determined that maximum deflection was a more critical factor in determining the overall design and was considered during the analysis and testing phases. During the manufacturing and testing phase of the frame construction, it became apparent that additional support would be needed to accommodate bending seen between the two front wheels. To account for this deflection, a wooden support that spanned the distance between the front spindles was mounted on top of the cart.
Brakes: Mounting the brake(s) to the real axle would be the most effective and easiest to fabricate/assemble. This is due to the rear axle only being composed of one wheel and one axle compared to the front. Through analysis it was ultimately determined that ATV brakes would be an effective solution to stop the cart. This is due to the confidence to assemble the cart and the calculations which determined that the cart would stop within the required max braking distance.
Usability: Within the preliminary design review, the hand controls for the throttle and brake system were determined to be the best design. The brake lever was a self-enclosed hydraulic system that was going to be mounted vertically on a steering lever, and a trigger from the drill was going to be rewired onto the opposing steering lever. Two other concepts that were considered were altering 1 pedal and 1 hand control, such as a brake pedal and a hand throttle or the other way around. The final design that was having the brake and throttle pedals located at the front of the vehicle.
Drive Train: The major factor in the decision to use a torque converter as the drive train was its ability to prevent stalling.The torque converter has a large torque ratio when first engaging and the angular momentum built provides a kick to get the cart moving. Initial calculations were completed for bike gearing in parallel for a backup option. This backup was not used as the torque converter was found to be highly capable for the needs of the cart.
Steering: For the steering subsection of our cart we chose to do Ackerman steering using levers to direct the cart. Since there was a requirement of not using traditional steering as well as using more or less than 4 wheels this was our best option. Through multiple NX models and building trial and error we settled on this design.
Mentor
Christopher Muir
Acknowledgments
This project was made possible with the help of Professor Christopher Muir and our lovely TA Seungju Yeo. Thank you Professor Christopher Muir for teaching the materials needed to understand and successfully complete this project as well as providing all instructions needed for this build. A deep sincere gratitude was also expressed for the University of Rochester’s Mechanical Engineering department for providing the materials, equipment and resources needed for this project to come together.
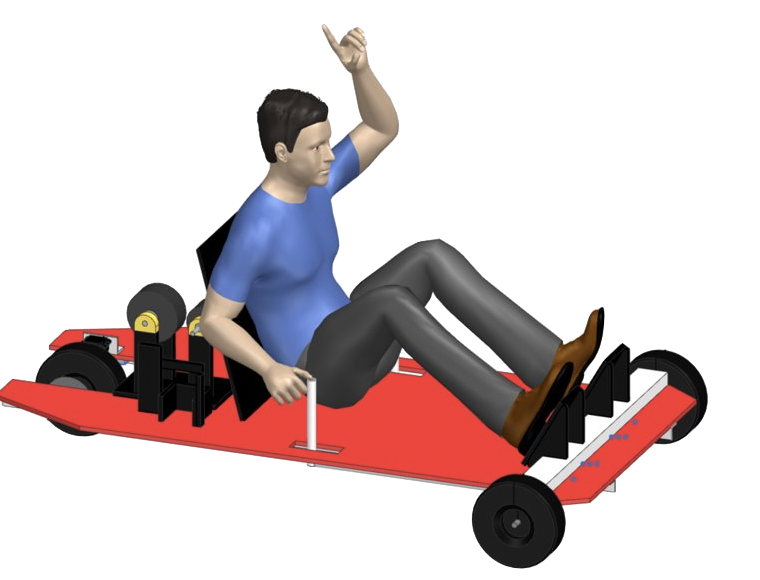