Team
- Anjana Seshadri
- Hailey Baker
- Preston Hollopeter
- Daphna Yaffe
Mentors
Chris Wolfe and Professor Matthew Yates
Abstract
A process developed by Xerox results in a waste stream of heptane and polydimethylsiloxane (PDMS), 7:1 by mass. Process scale up and complete separation of PDMS from heptane is desired. Previously, Team Nimbus (2021) had successfully designed a batch system to extract heptane from PDMS. As a comparison, a semi-continuous process was built and further investigated.
Introduction
The PDMS used by Xerox to create other desired polymer products has a viscosity like molasses (at 25°C). PDMS easily dissolves in nonpolar solvents, such as heptane, which greatly reduces its viscosity.
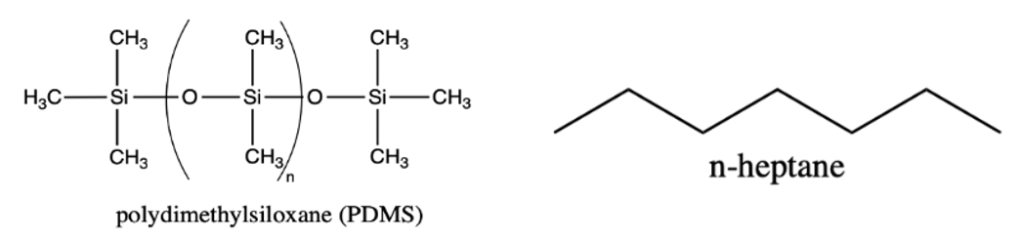
Supercritical CO2 extraction is commonly used to separate binary mixtures for high purity through solvation. The solvent capabilities of CO2 depends on its density, which can be manipulated by pressure and temperature. Team Nimbus demonstrated that CO2 can solvate heptane at 1300 psi and 34 C, resulting in a purified polymer [1].
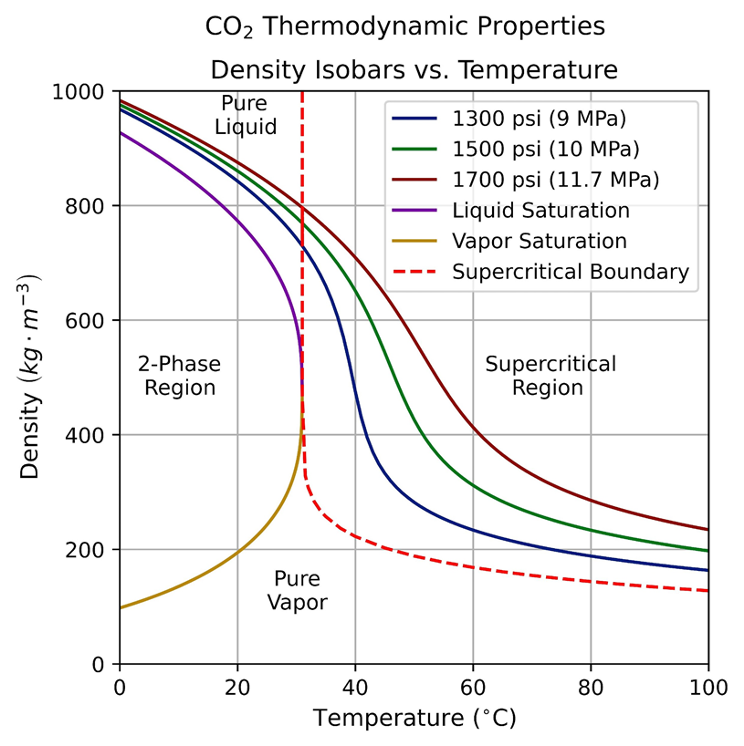
Purity of PDMS was measured by viscosity. Rheology is a highly precise method for viscosity measurements. The calibration curve for varying mass ratios of Heptane:PDMS is shown in Figure 3.
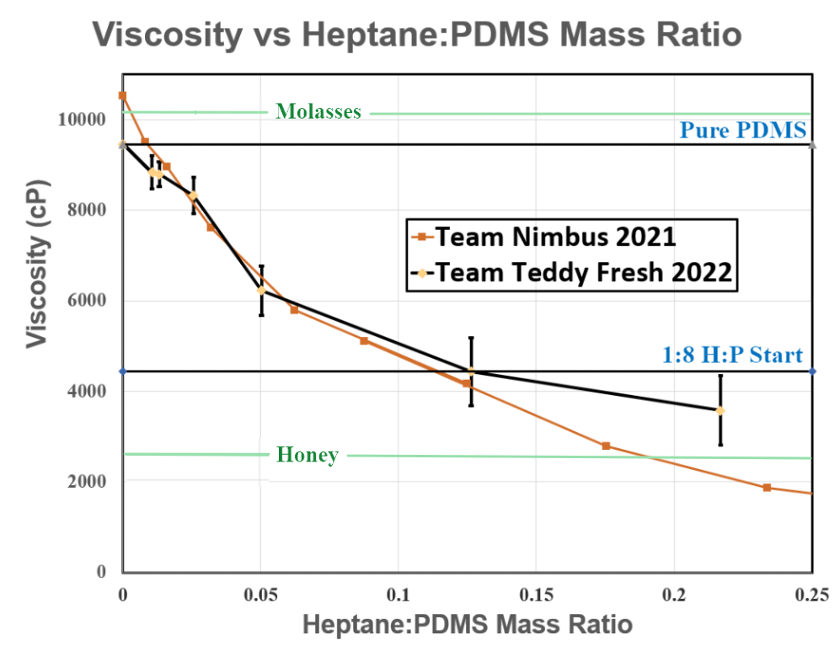
Last year, Team Nimbus created a batch system that successfully extracts heptane from PDMS and results in a polymer that is 99.09% pure.
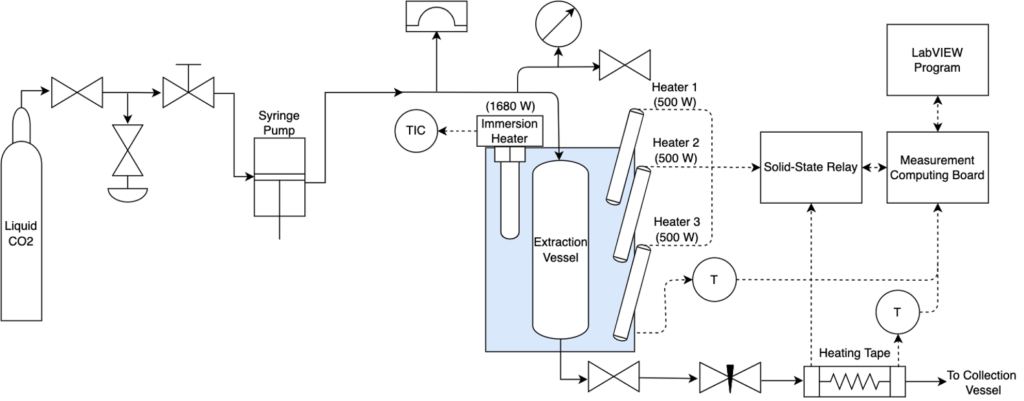
Hypothesis
A semi-continuous flow of CO2 and an increased interfacial surface area between CO2 and the sample will create a larger driving force for the mass transfer from the PDMS phase to the CO2 phase than in the batch system.
Methods: Semi-continuous system
The semi-continuous system design was heavily influenced by the batch extractor, with modifications to allow for semi-continuous operation (Figures 5,6).
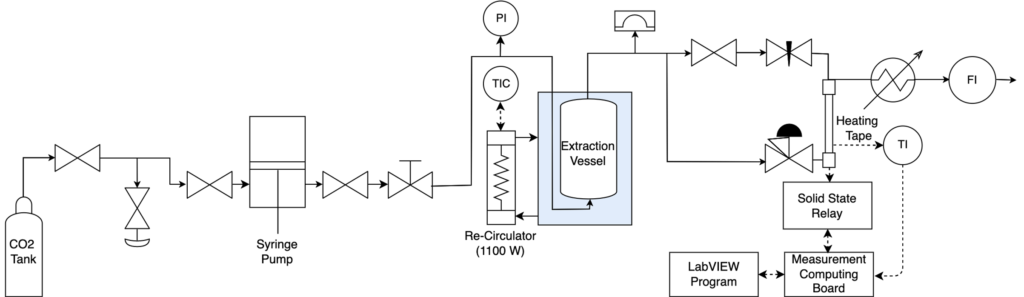
System Overview:
- Back pressure regulator and syringe pump to pressurize the system while allowing for good control over both pressure and flow rate of liquid CO2
- Temperature-controlled water bath to maintain the extraction vessel temperature
- A 1:8 heptane:PDMS sample was loaded into the extraction vessel and flushed with supercritical CO2
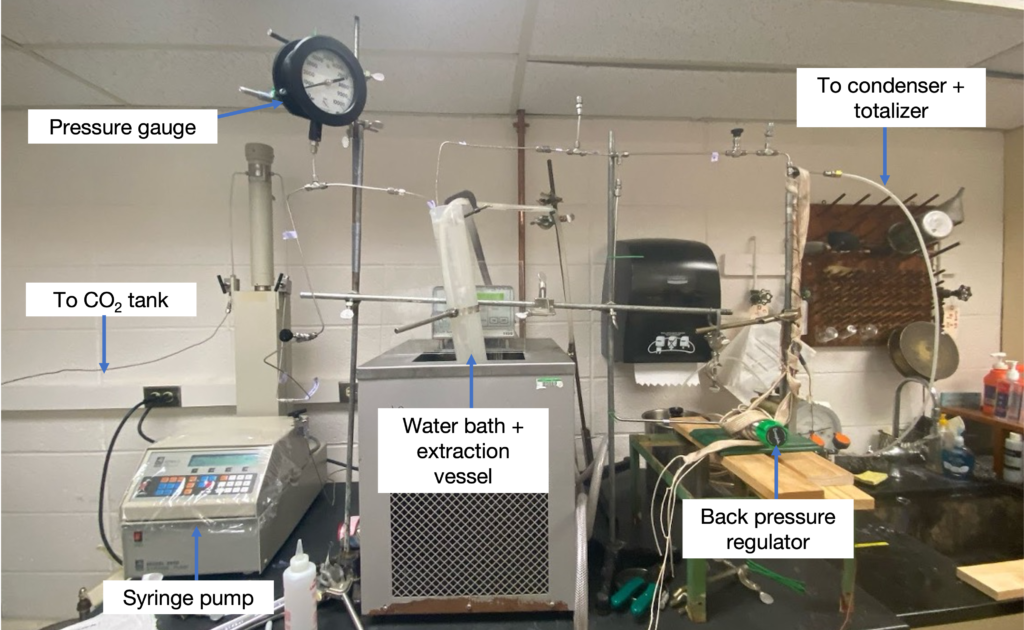
- A metal mesh was inserted into the entry fitting of the vessel to act as a sparger for the CO2 (Figure 7)
- The separation of heptane and CO2 occurred in the condenser, where low temperatures decreased the solvent capabilities of CO2
- The purified PDMS was collected from the extraction vessel
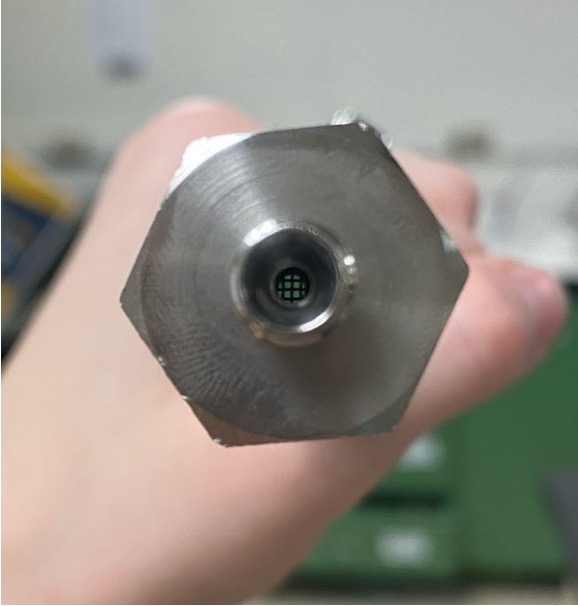
Methods: Batch System
- Team Nimbus’ batch system was used to test the hypothesis that the soak time and flush rate impacted the resulting purity of the PDMS-heptane mixture
- Conducted a Design Of Experiment (DOE) to analyze the effects of soak time and flush rate on purity
- Trials also supported the hypothesis that PDMS and CO2 were miscible under supercritical conditions (Figure 8)
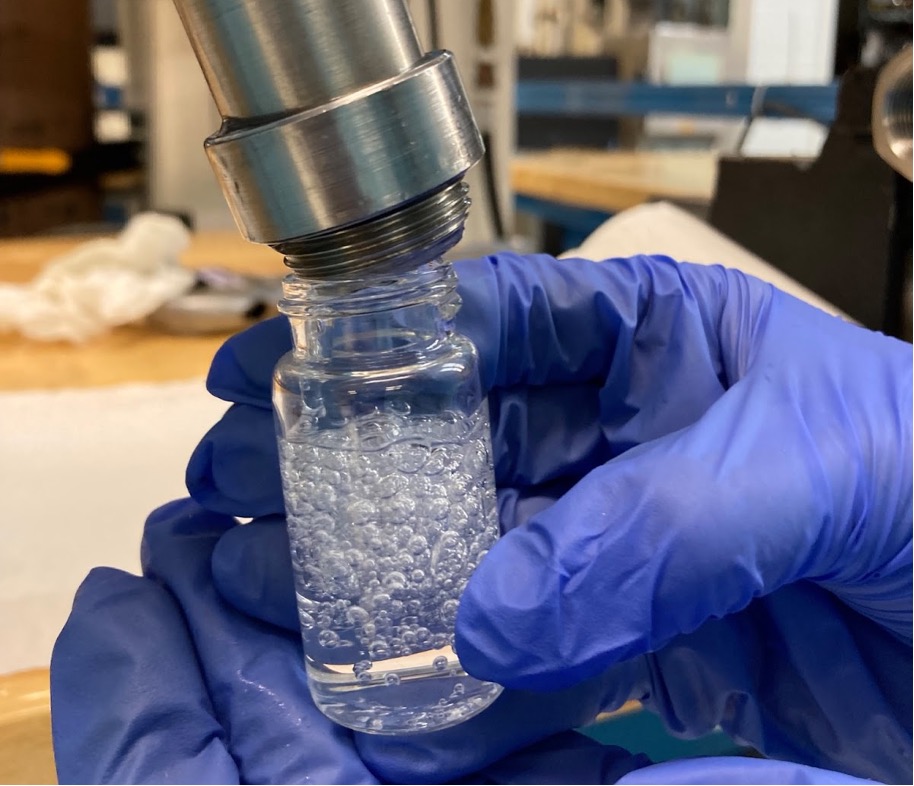
Results and Discussion
- Results for the DOEs performed on the semi-continuous and batch systems are shown in Tables 1 and 2, respectively.
Table 1. Semi-continuous system DOE results
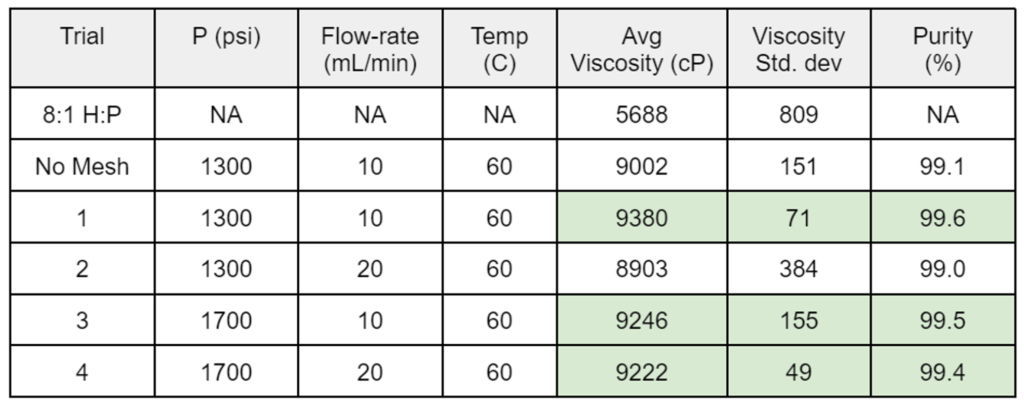
Table 2. Batch system DOE results
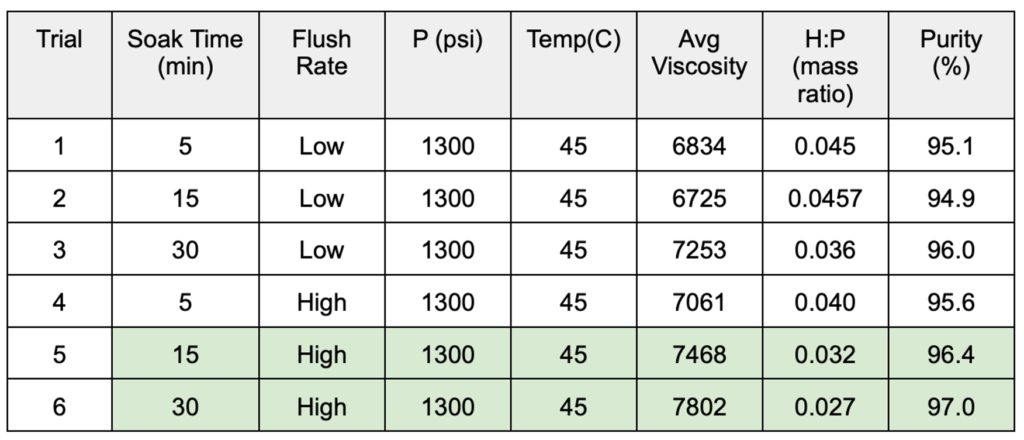
- A semi-continuous setup with a mesh insert to increase the interfacial surface area between CO2 and the sample did yield a greater mass transfer from the PDMS phase to the CO2 phase per volume of CO2 used.
Conclusions and Future Work
The semi-continuous system successfully extracted heptane from the 1:8 Heptane:PDMS mixture and yielded a higher purity product than the batch system per volume of CO2 used. The addition of a mesh to the vessel likely increased the extraction of heptane. Due to low yield and poor pressure control, however, the current semi-continuous system is not viable for scale up until these factors have been addressed.
Possibilities for future work include:
- Further investigation of the semi-continuous system to find optimal extraction conditions
- Investigation of other parameters (temperature, vessel diameter and length)
- Exploring a wider range of operating pressures and flow rates
- Incorporating a static mixer into the vessel
- Investigate ways to increase the lifetime of the system, reduce loss of sample, and prevent clogging of the valves and pipes with PDMS
Acknowledgements
The team would like to thank our sponsor, Chris Wolfe from Xerox, our faculty advisor, Professor Yates, and Professor Lawton, Professor Kelley, Professor Juba, Clair Cunningham, Mason Garlatti, Jeffrey Lefler, Quinton Dang, and Mark Volkin for their support, encouragement, and assistance with this project. We would also like to thank Team Nimbus (2021) for their careful documentation of their work on this project last year.
References
1. Team Nimbus, 2021, University of Rochester Department of Chemical Engineering