Team
- Kelsey Lee – Document Handler
- Joseph Lugten – Customer Liaison
- Icel Sukovaty – Project Coordinator
Mentor
Prof. Jaime Cardenas
Abstract
The META360 Hybrid Refractive-Metalens Design project seeks to enhance the current Circle Optics 360º field-of-view stitch-free camera system using novel meta-optics technology. Our goal is to evaluate the use of meta-optics in a hybrid lens design using Synopsys’ MetaOptic Designer (MOD) software, aiming to incorporate one metalens into a current Circle Optics visible-wavelength design to reduce size and weight and to improve performance of the design. We explore a method of using electric field modeling as inputs to MOD to bypass computation limitations of larger conventional lenses in MOD.
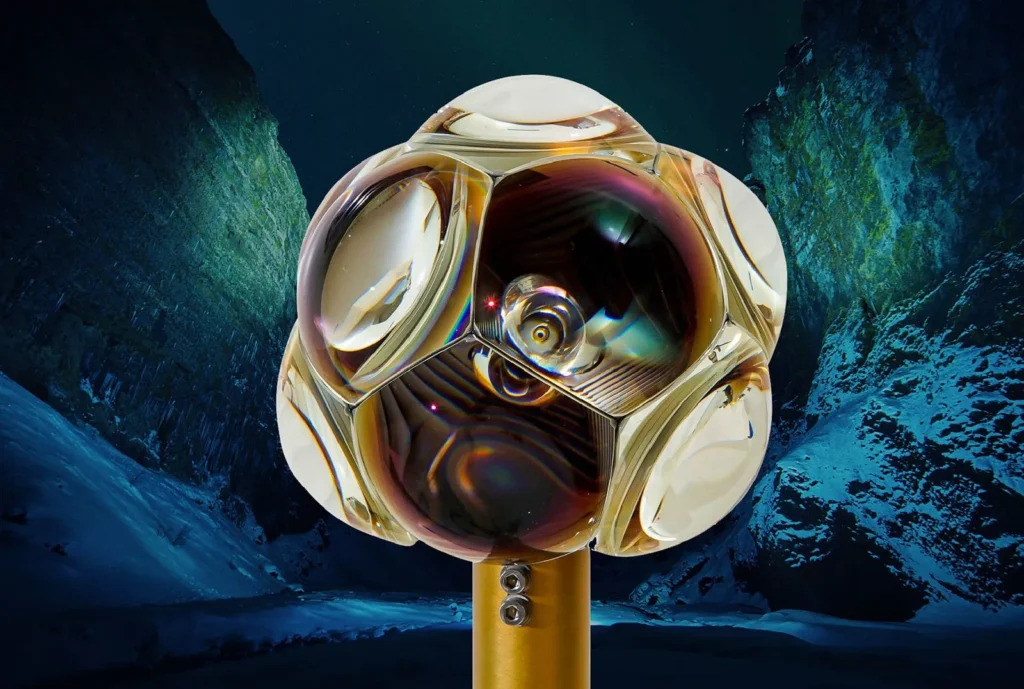
Circle Optics
Circle Optics is a Rochester based company that designed the world’s first stitch-free 360° field-of-view multi-camera system. This design controls parallax between adjacent camera modules to achieve a high-quality image with minimal distortion. This has applications in a variety of industries, including robotics, drones, aerospace, and entertainment.
Metalenses and Synopsys’ MetaOptic Designer (MOD)
Metalenses are an emerging technology using sub-wavelength structures to manipulate light in amplitude, phase, and polarization. These metalenses are much smaller and lighter than traditional refractive lenses. Metalenses are traditionally designed manually and requires in-depth understanding of its physics and extensive design experiences. Synopsys’ new MetaOptic Designer software aims to automate the design process, taking in user specifications to generate metasurfaces for optimal performance.
Our Design Methods
Two methods were explored for creating a hybrid refractive/metalens design. The ideal method is to insert the existing lens design into MOD, then optimizing for a metasurface. As a backup method, an electric-field profile can be generated at the desired metalens surface and used as an MOD input to design the metalens.
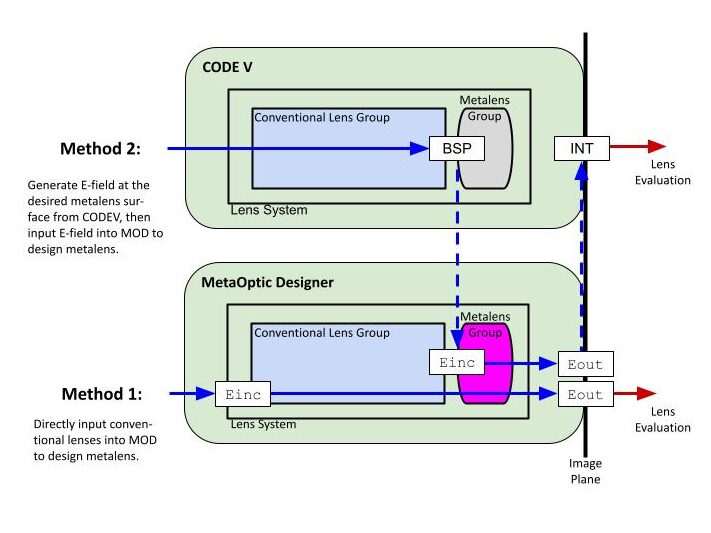
Method 1: MOD-only Design
We aimed to input the existing lens directly into the MOD software and optimizing for the metalens surface. This method is not viable due to computation limitations in MOD. Lenses with diameters on the scale of mm requires a large amount of RAM to compute due to the large number of nano- structure periods across the metalens. As a result designing the desired hybrid lens using this method is not possible.
Method 2: Electric Field Modeling for MOD Input
The second method aimed to bypass some of the current computation limitations in MOD by modeling the electric field after light propagation through the conventional lenses. The electric field profile after the last conventional lens surface is generated using CODE V Beam Synthesis Propagation (BSP) and used as the input for MOD. The metalens is then optimized in MOD.
Interfacing CODE V with MOD – A Design Example
We demonstrate an example of a plano-convex singlet with the flat surface as the metasurface is used to demonstrate the above two methods and their equivalence.
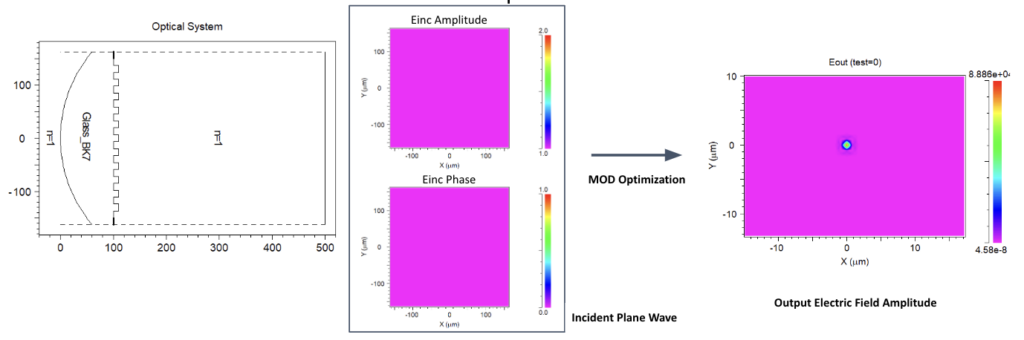
This design is completed using only MOD. Glass information and an incident plane wave is inputted into MOD. The desired output field is a Airy spot, and relative focusing efficiency is 0.9625.
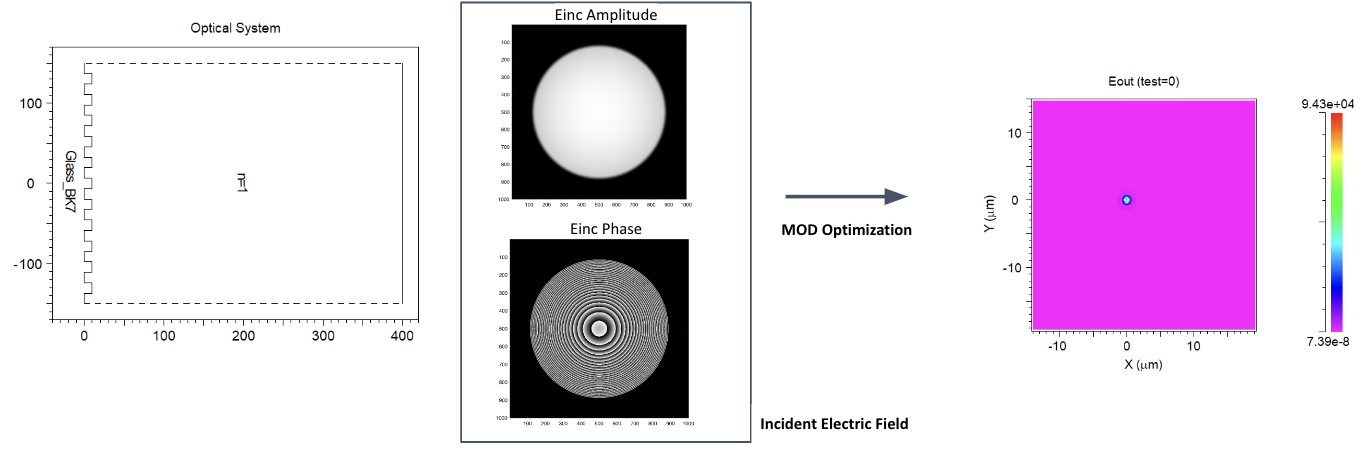
A second design is completed using the CODE V’s BSP. The data is converted into an RSoft compatible incident electric field file, which is then used for the MOD optimization. The relative focusing efficiency is 0.9625.
Then, to evaluate the designed lens in CODE V, an interferogram file is created using the phase profile of the metasurface transmission, and it is placed at the planar surface of the lens in CODE V. After refocusing with the metasurface, the improvement in the MTF becomes apparent. Without the metasurface, the lens performs at 50% MTF at 95 lp/mm, but with the metasurface, the performance increases to 50% MTF at 122 lp/mm.
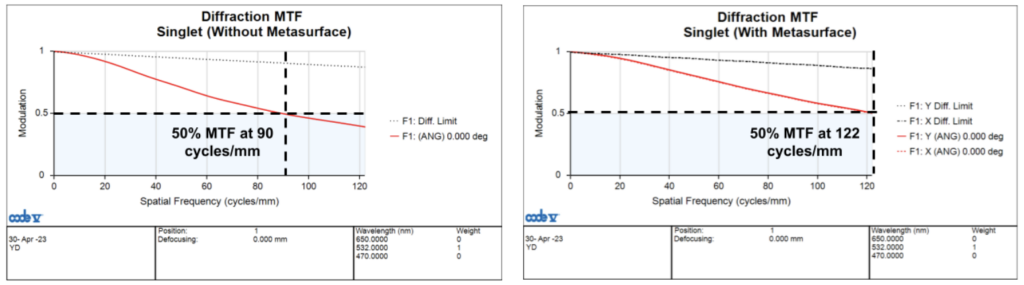
The singlet example demonstrates the process of transferring the optical design to and from CODE V and MOD.
Manufacturability of Metalenses
Metalenses require precise nanofabrication to create the required meta-atom structures. The size of these structures depends on the wavelength of light used, with smaller structures being required for shorter wavelengths. As fabrication techniques have improved, metalenses have been demonstrated for shorter and shorter wavelengths, with recent research proving the viability of visible wavelength metalenses. For these visible metalenses, structures are 100-350 nm wide.
Electron beam lithography is the most common fabrication technique for metalenses, due to its high precision and versatility. However, this versatility is a limitation when it comes to high-volume production.
Photolithography and nanoimprint lithography are two alternatives that are suitable for mass production. Photolithography is already being used to make real-world metalens systems, and several companies are developing nanoimprint lithography techniques as a more affordable but still precise method.
Conclusions
E-field modeling for CODE V to MOD interface is a viable option in pushing the current computation limit for creating a hybrid refractive-metalens design. However, this is dependent on the accuracy of the E-field profile generated after propagating through the optical system. If this is done using CODE V Beam Synthesis Propagation, sampling and aliasing can be problems especially for the phase profiles at non-focusing surfaces.
Some future steps to ensure accurate phase and field profiles can include using a combination of phase retrieval methods (which only requires accurate amplitudes and PSF) and computational ABCD propagation.
No matter what method is used, hybrid refractive/metalens design is fundamentally very difficult. Metalenses are typically no larger than 1 mm in diameter, while refractive lenses rarely get this small. This means that combining the two into one system is often impractical. The most obvious solution is to make larger metalenses, but this gets computationally very expensive, as a 1 mm diameter metalens has millions of features. This results in large files and long optimization times. Additionally, traditional lens design theory and software models light as a ray, which allows it to optimize systems quickly. Metalenses need a wave-based model of light, so even the refractive elements in hybrid systems must be designed with the more computationally expensive wave-based model.
These computational limitations make the development of hybrid refractive/metalens systems challenging. While the area certainly has potential, current design tools are not yet capable of performing the required analysis.