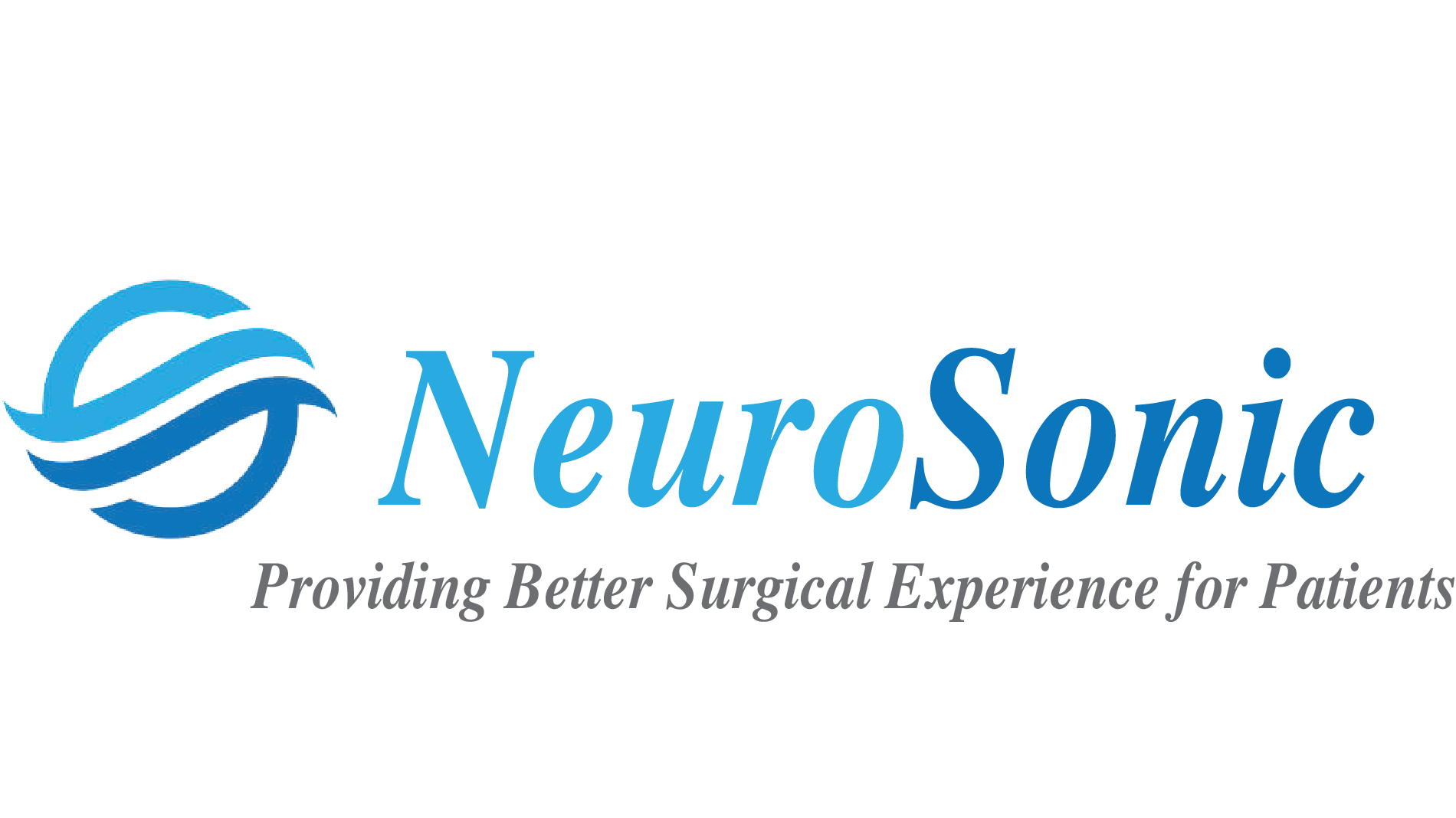
Team

Kee Bark
B.S. Biomedical Engineering
M.S. Biomedical Engineering ’23
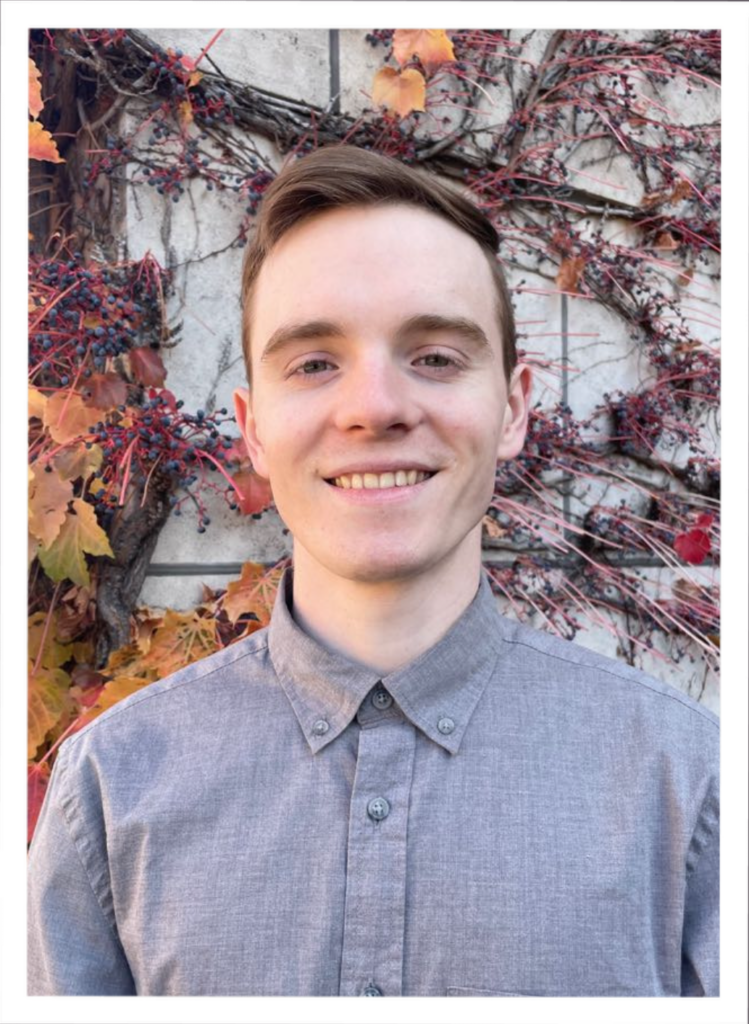
Jack Bates
B.S. Biomedical Engineering
M.S. Biomedical Engineering ’23
Project Summary
Our project, involved developing a neurosurgical medical device. Our mission was to provide neurosurgeons and hospital purchasing agents with patient hearing protection solutions for brain surgery. Our team successfully designed a solution to reduce noise generated by the cranial drill during brain surgery. We believe our solution will provide hospitals and neurosurgical practices to improve patient care, protect patient hearing, and prevent medical malpractice lawsuits.
Project Background
BioDesign Statement: A way to minimize patient discomfort and risk of hearing loss during craniotomy surgical drilling.
Problem: During awake brain surgery patients experience significant discomfort due to the noise generated by cranial drilling. Further research studies indicated that cranial drill noise can induce permanent hearing loss in some patients. Hearing loss costs individuals over $297,000 throughout their lifetime and is associated with lower employment rates, lower worker productivity, and higher healthcare costs. Traditional earplugs are ineffective because drill noise travels directly through the bone of the skull. Therefore, neurosurgeons are unable to effectively provide patients with protection using current noise reduction strategies. This also poses a risk of medical malpractice lawsuits for patient hearing loss, which can cost neurosurgeons and hospitals over 1 million dollars in awarded damages.
Clinical Observation: The clinical observation of this problem occurred in a deep brain stimulation (DBS) insertion surgery, in which the patient was awake. The surgeon used a surgical cranial drill to make a small hole in the patient’s head. But, the problem was that the drill was uncomfortably loud for patients during its use. Further research revealed that the noise is conducted through cranial bone to reach the inner ear, which is why earplugs are not an effective solution [1]. We aim to target general craniotomy procedures that use a cranial drill because even if the patient is not awake there is still noise being generated that may induce lasting hearing damages [2].
Initial Concept
The technology we are designing is intended to reduce the drill induced noise transmitted to the patient’s inner ear. The main concept we are pursuing involves using active noise cancellation (ANC) techniques to reduce the drill noise conducted through the cranial bone by emitting counter vibrations transcutaneously. This general ANC concept is depicted in Figure 1 below.
Our initial concept of the device is composed of a recording system, control system, and stimulating system that will contact the patient’s intact skin on their head. The device will function by using a bone conduction recording element such as an accelerometer that will record the cranial drill noise conducted through the patient’s skull in real time. A control system will then process the cranial drill noise bone conduction signal and send an opposing signal (180 degrees out of phase) to a vibration emitting system. The vibration emitting stimulation system will then cancel the cranial drill noise signal before it reaches the patients inner ear through emitting an opposing signal transcutaneously. This system may consist of a vibrator such as a piezoelectric actuator. This concept is depicted in Figure 2 below.
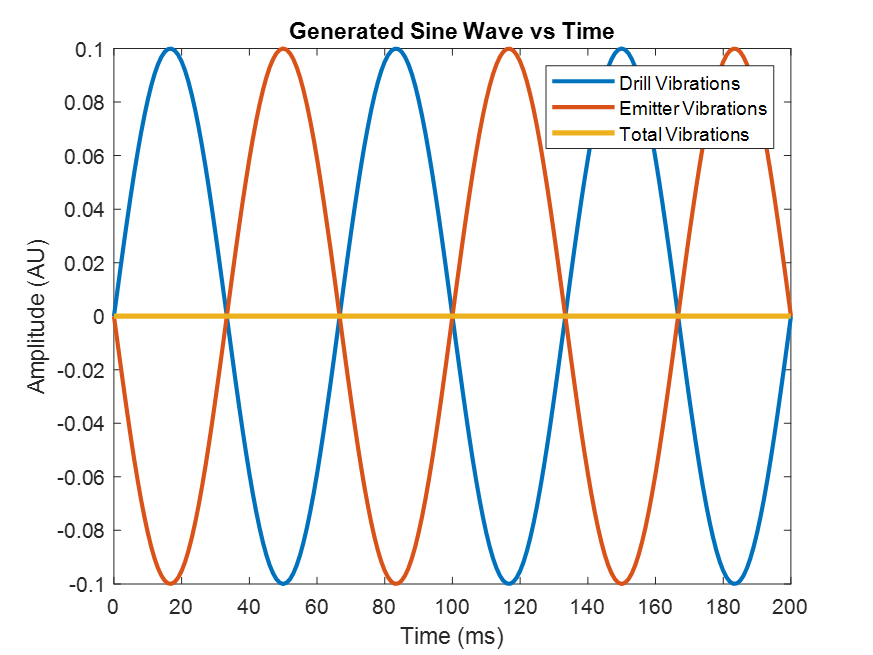
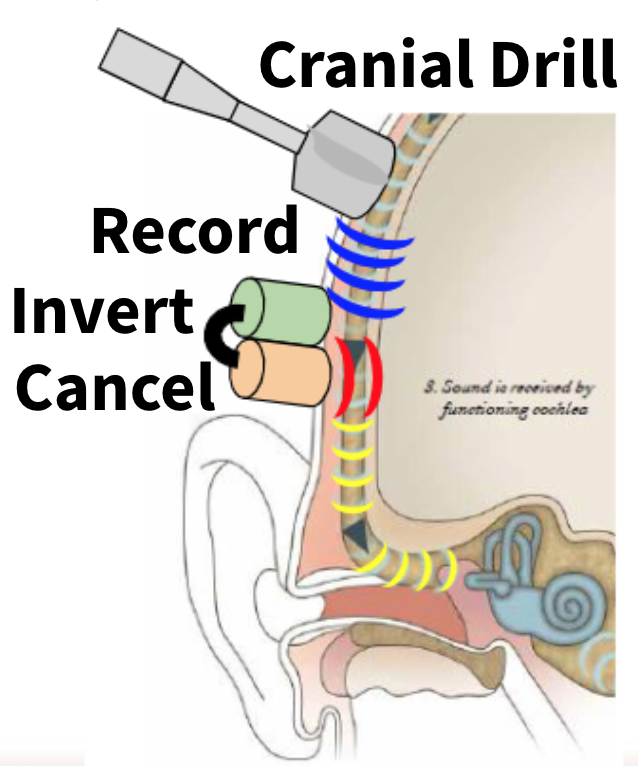
Testing
Feasibility Testing
Quantify vibration reduction on a table-top board model
- Computer drives BC transducers/speakers
- Accelerometer (ACC1) measures vibration amplitude
- ANC = inverted BC2
- Control = inactive BC2
Results
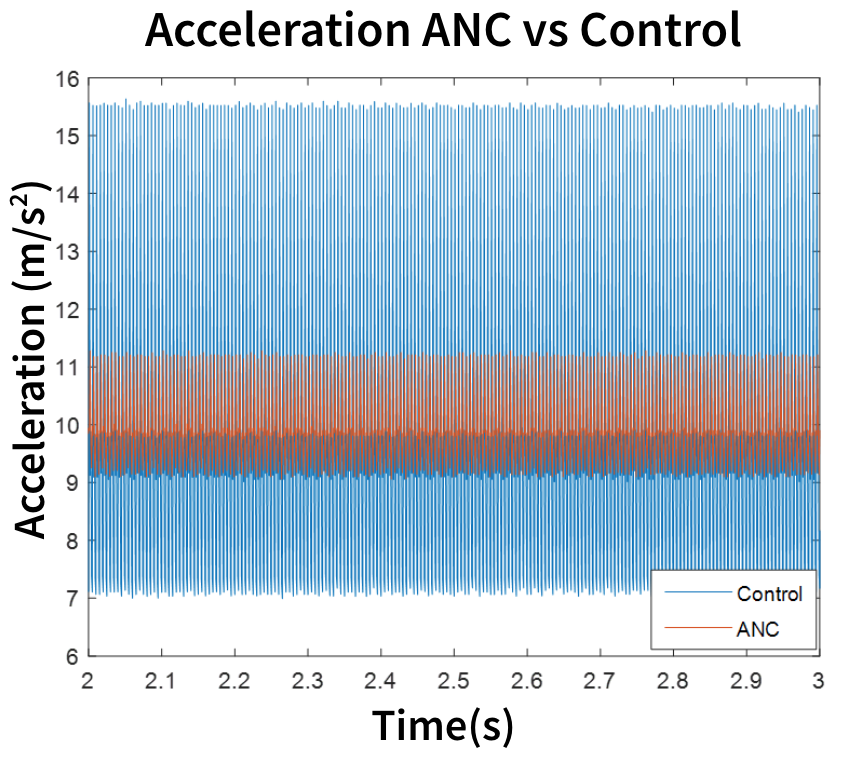
Conclusion
We can achieve 65% reduction in vibration by using a BC vibrator (BC2) with consistent amplitude and 180 degrees out of phase from the BC1 vibrator signal on a table-top board model.
Real-Time Testing
Quantify vibration reduction in real-time on a table-top board model
- Computer drives BC1 (drill) transducer
- ACC2 (ear) measures vibration amplitude
- ANC = ACC1 measures BC1, inverts & drives BC2
- Control = inactive BC2
Results
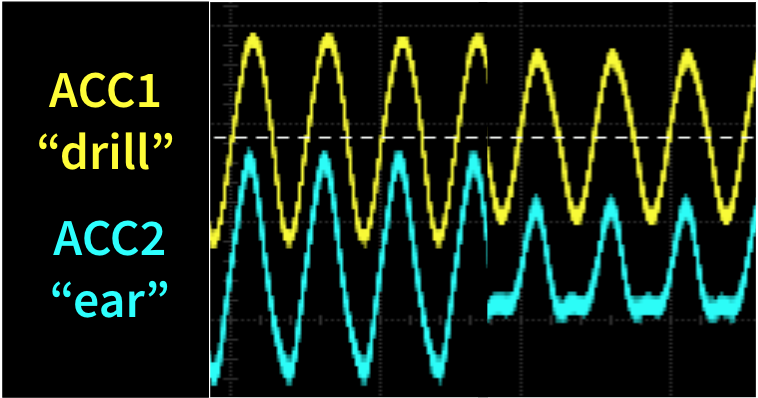
Conclusion
We can achieve 50% reduction in vibration by using an accelerometer (ACC1) to capture the signal from BC1 “the drill”, invert it, and use that signal to drive BC2 in order to cancel the vibrations from BC1 on a table-top board model.
Real-Time Cranial Drill Testing:
Quantify vibration reduction in real-time on a table-top board model using a cranial drill
Most recently we used our system as described in the solution section to cancel out the vibrations from a cranial drill on a table-top board model. This system is the same setup as in the Real-Time Testing, however BC1 is now replaced with a surgical cranial drill that is used to vibrate the board.
Results
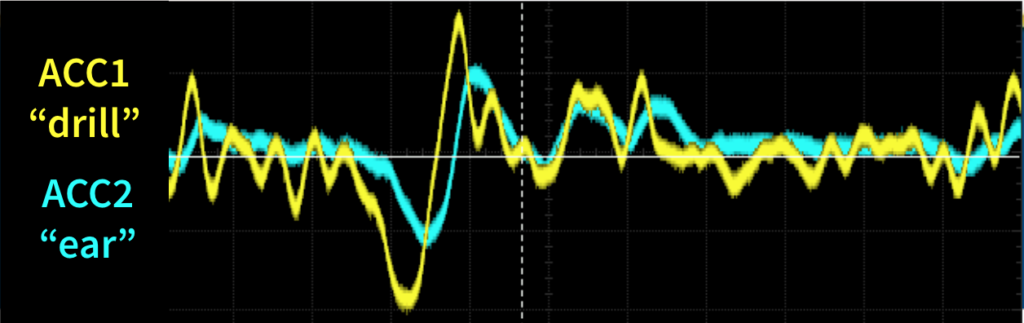
Conclusion
When using a perforator drill bit with a surgical cranial drill at 40,000RPM our ANC system can achieve 40% reduction in vibration.
Product Design
We envision our final product to be a reusable medical grade, bone conduction headset. This headset will feature a single-use disposable coverings that prevent contamination between patients for different surgical procedures. The single-use coverings are a clear sleeve composed of surgical drape grade material designed to enclose the headset during its use in surgery. One promising location the device may interface with specifically is the mastoid process. The physical attachment mechanism is still in development, but may consist of a headband or adhesive adaptor similar to the ADHEAR System (K172460).
Our technology will able to achieve 50% reduction in vibrations of a surgical drill on a skull bone model. Our team will work to achieve a greater than 50% reduction in surgical drill vibrations, design improvements to the technology, and work closely with neurosurgeons to fix problems. We believe our headset will easily be placed on a patient during brain surgery by the operating room surgical team. The design of the headset is shown in the image below.
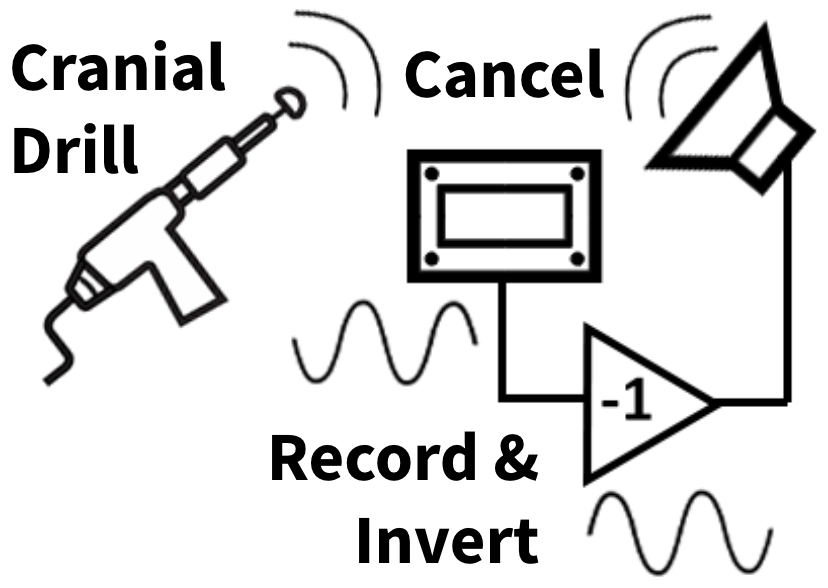
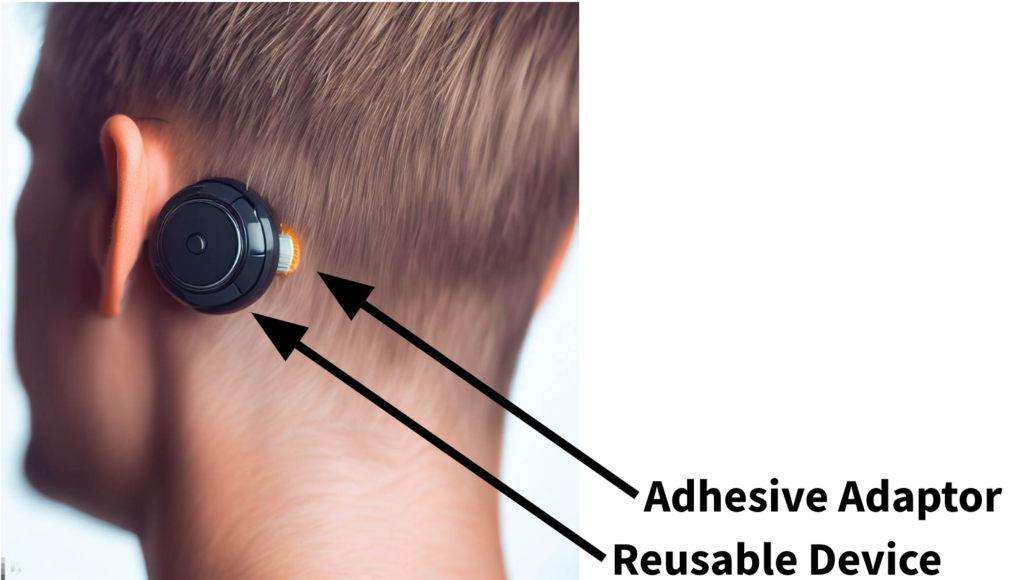
Key Design Features
Real-Time Drill ANC | Reduce drill vibrations by 50%
Reusable Device | Low cost
Adhesive Adaptor | Quick placement & low surgical interference
Single-Use Coverings | Prevents contamination
Competitive Advantage
Our competitive advantage is that it provides solution that is easy to integrate, saves time during surgery, and is overall cost effective when compared to competitors/current approaches to solving the problem. For example, current surgical approaches such as reducing drill holes, lowering the drill use time, and performing the awake-asleep-awake technique all can add on an additional 30 minutes or more to the overall surgery duration. The competitive matrix below will outline key attributes of our product and our competitive advantage and positioning.
Cost | Surgical Time | Surgical Complication | Efficacy | |
Our Device | $440 per device, reusable$50 single-use | 1 minute to integrate | None | Effective in reducing conduction of drill noise through bone |
Traditional Ear Plugs | $5 per device, Not reusable | < 1 minute to integrate | Does not allow for communication between surgical team and patient | Does not account for conduction of noise through bone |
Surgical Drills | $5,000-$50,000, reusable | No additional time | None | Does not account for conduction of noise through bone |
Surgical Drill Bits | $500-$800 per surgery, not reusable | Takes significant more time> 30 minutes | None | Does not account for conduction of noise through bone |
Putting Patient to Sleep Method | No significant increase in sedation costs | Takes significant more time> 30 minutes | Can hinder communication between surgical team and patient | Noise is still conducted through the bone |
Future Work
Design Refinements: Currently, working prototype of the product was developed. However, our device needs to be refined with upgraded device equipment, and needs to further meet DFM standards.
Refined Testing Methods: We believe we must undergo rigorous cadaver skull model testing to ensure our device is safe and effective. We will further need to conduct usability testing, performance testing, and clinical testing.
Others: Before this device is marketed, we need to secure regulatory clearance and a patent. We will also look for SBIR funding and aim to license our technology to major surgical drill manufactures such as Medtronic, Stryker, ConMed for an exit.
Acknowledgements
Our team would like to personally thank each individuals for their guidance and support in our project:
Greg Gdowski, PhD
Amy Lerner, PhD
Jonathan Stone, MD, MSe
Marty Gira
Mahllet Beyene