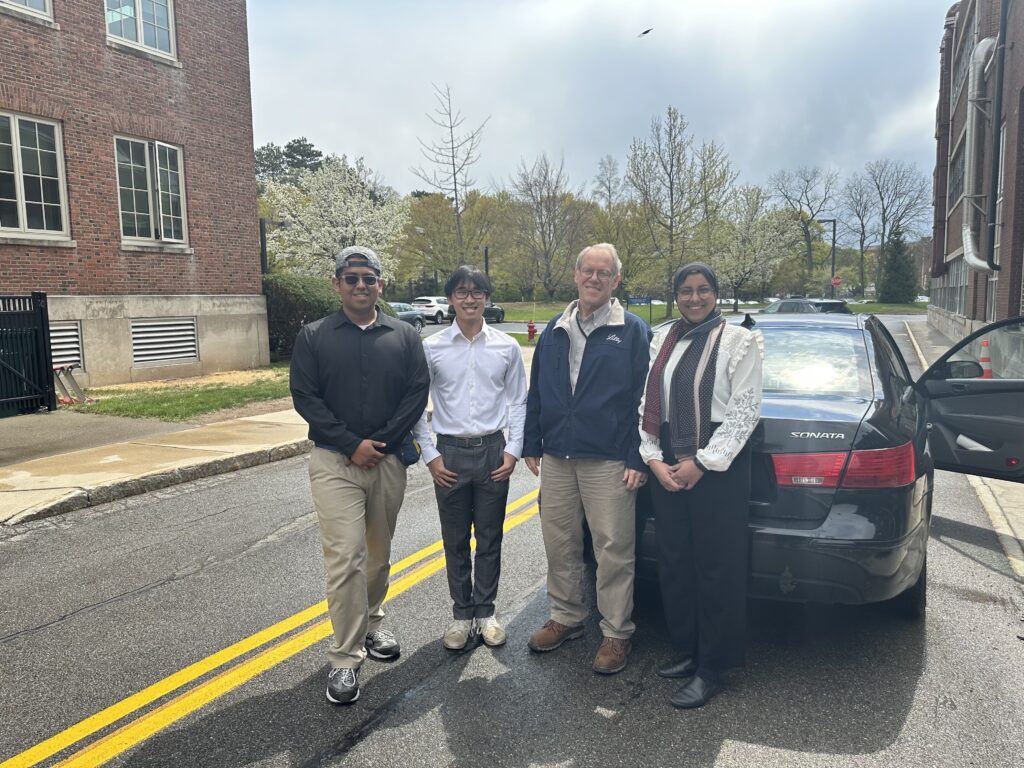
Team
- Andrew Rojnuckarin
- Brian Garcia Hernandez
- Niera Bakr
Sponsor
SPX Flow: Dr. Richard Cope
Mentors
Doug Kelley, David Foster
Abstract
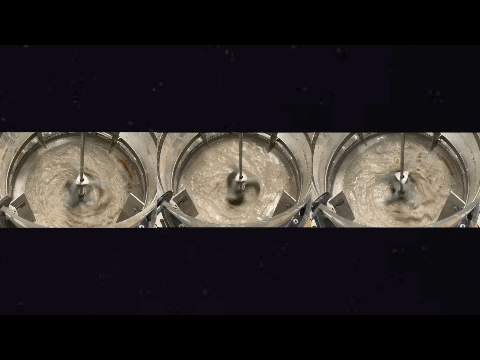
Slurries are semi liquid mixtures that typically contain solid particles suspended in a liquid medium. Slurries are commonplace in many classic chemical engineering settings including fluidized beds, reactions with precipitates and polymer manufacturing. Many problems that engineers face when dealing with slurries is caused by the deposition of solids out of the liquid phase during mixing and draining of large tanks. This deposition can result in solid heels accumulating at the bottom of tanks and in drainage pipes that could result in loss of product and damage to equipment.
One current industrial solution to this problem is placing an impeller closer to the bottom of the mixing tank. This auxiliary impeller is known as a tickler. Ticklers prevent heel formation from occurring and allow for most, if not all, material to drain through the tank. The goal of this project is to design a system to test different tickler impeller configurations to optimize slurry draining performance. By the end of the Spring 2023 semester, the system must support a mixing tank with a shaft that can mount a main and a tickler impeller. Material must be able to drain out of the tank from the bottom and the system must be able to quantify the performance of the tested configuration. Performance is based on the rate of draining and heel mass.
Introduction
Slurry draining is an important part of many manufacturing processes. For instance, in drywall manufacturing, a slurry of gypsum and water are mixed before being drained onto flat sheets. Here, drainage must be properly characterized to control product quality and consistency. Tickler impellers are small impellers design to be placed at the bottom of a draining tank to agitate fluid near the drain thus suspending solids and shearing heels. It was proposed that the drainage of a fluid from an open tank could be modeled using a transient response function derived from Bernoulli’s Equation.
However, Initial trials suggested a significant decrease in rate occurring mid-way through each drain. This behavior is likely a result of air entrainment via vortexing.
System Overview
The final system consisted of an automated mass scale to measure the decreasing weight of the tank as the slurry drained out. Gypsum was used as a slurry solid, and was mixed with 8 gallons of water at 15 and 30 wt%. Samples were collected at the outlet in increments to determine the density changes over time.
Tickler Comparison
To remove the heel, SPXFlow provided 3 designs: KT-3, RAI and RAO. The tickler’s height from the drain had an inverse relation with heel mass. Three more ticklers were designed. Although each new tickler was effective at heel removal, none could match the drainage speed that the KT-3 had.
Vortex Breaker
Air entrainment was observed to be a significant contributor to slow drain times. A scatter plot was generated of drain time and entrainment severity and a strong positive correlation was shown between the two variables.
Vortex breakers are typically mounted to the bottom of the tank to reduce air entrainment. A novel round vortex breaker was mounted to the motor shaft to support tickler engagement and mitigate air entrainment.
Density Data
The data shows that the density of the slurry, and thus the concentration of the gypsum in the slurry, remains fairly constant as its drained from the tank. This suggests that all ticklers do well at distributing the solid components throughout the drained slurry. Although some variance is observed, no clear patterns were identified.
Main Impeller Effects
Based on the data, the radial main impeller provides a faster drainage rate at the cost of increased heel mass. This may be due to the high power number of the R100 requiring a lower RPM which may be too slow to suspend solids during mixing. Ticklers may not be able to shear against the stronger static friction forces of the developed heel.
Conclusions and Future Work
The collected data suggests that the KT-3 is the most effective impeller at mitigating heel mass relative to operation time. The KT-3 is most effective when placed as close to the drain as possible. To mitigate air entrainment, a vortex breaker can be mounted to the motor shaft. Future work with regards to this project could involve designing new tickler impellers, working with different power consumptions, working with different slurry compositions, pumping the fluid back into the tank using a centrifugal pump, and computational modeling.
Acknowledgements
We would like to extend our gratitude to our mentors and advisors who helped us during the course of this project. In particular, Dr. Richard Cope from SPXFlow, our two faculty advisors Professors Doug Kelley and Dave Foster, our teaching assistant Hung Nguyen, and the rest of the ChE Senior Design faculty including Melodie Lawton, Mark Juba, Clair Cunningham, Mason Garlatti, and Jeff Lefler, as well as James Alkins at Rettner.